Process makes the Difference
Hygienic Cleanliness for Food Industry – Machine-based COP Cleaning
Safe Food in the EU
Within the European Union, food companies must “ensure that the food they place on the market is safe at all stages of production, processing and distribution”.
And yet, despite all due care, there are precautionary recalls of individual batches that may be contaminated with germs or bacteria and could be harmful to health.
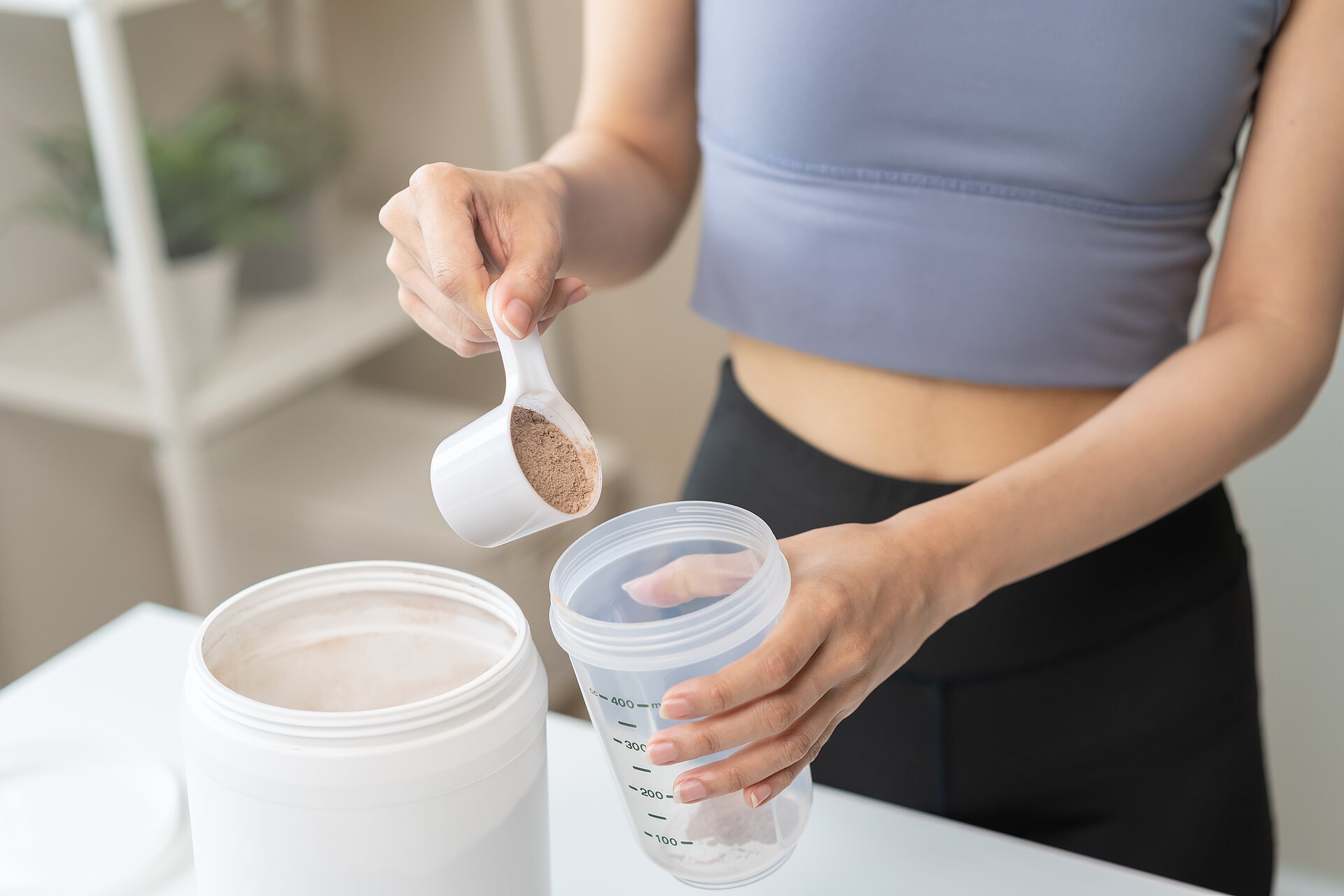
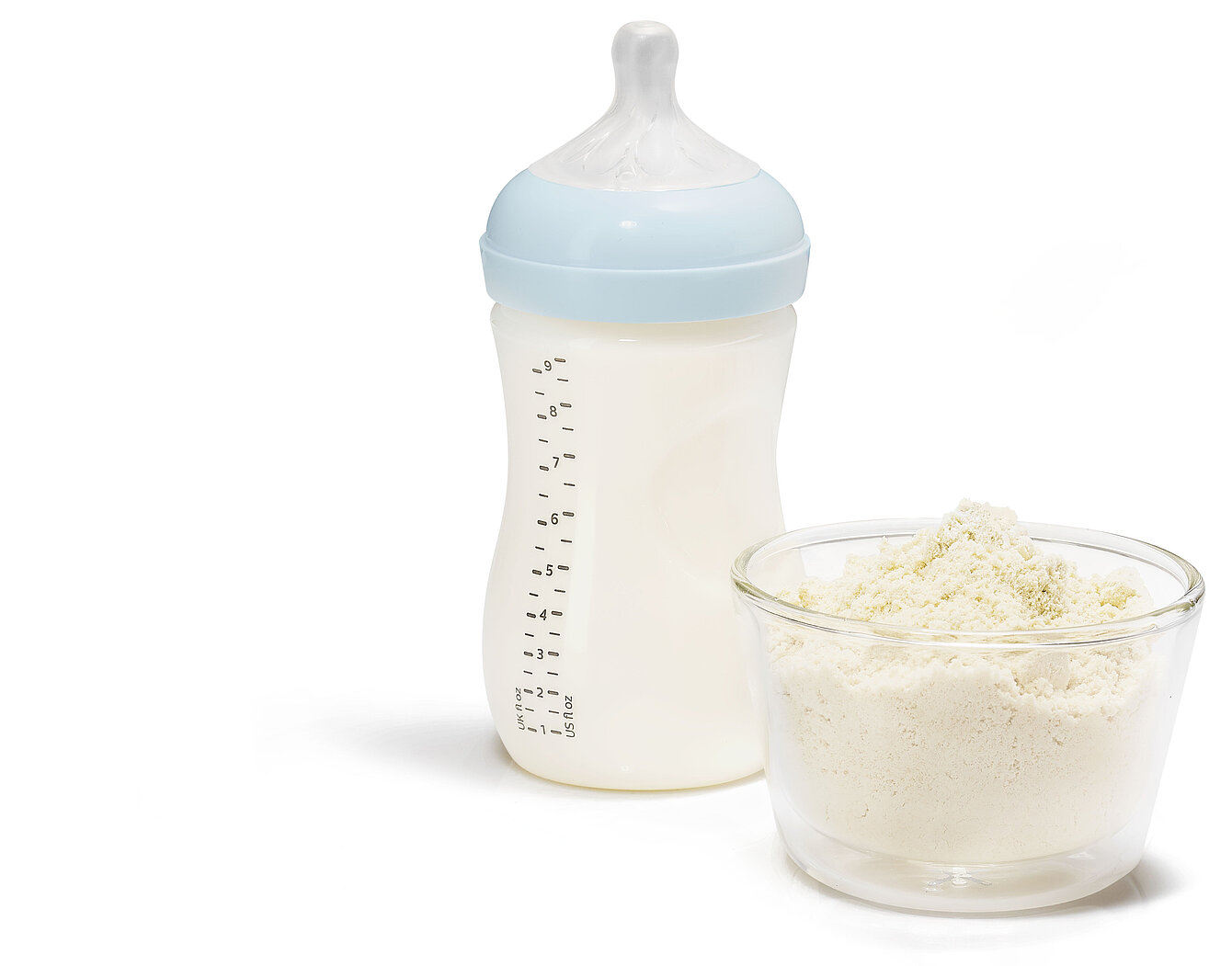
Minimal Irregularity, maximum Media Coverage
Precautionary, individual batches, may be contaminated: consumers tend to ignore this in their perception. Even if the contamination is not caused by the manufacturer, but by another company in the process chain as part of a “differentiated level of responsibility”:
But who really bothers to ask critical questions?
A recall is associated with the manufacturer and the brand.
This results in critical coverage and even a social media "shitstorm. For example, when disinfectants or MOSH are found in independent product testing. These saturated mineral oil hydrocarbons can get into food through lubricants used in the manufacturing process. In minimal amounts and not harmful to health.
But, as explained: Too much information for a snappy headline or a hate post.
Focus: Cleaning Processes
But how can contamination be eliminated as far as possible?
It is worth taking a closer look at the cleaning process. An industrial cleaning process explicitly designed for this highly sensitive industry could ensure that product-bearing parts are always clean and residue-free. However, the introduction of a new process in food production involves a great deal of effort – validation, qualification – and reluctance is quite understandable.
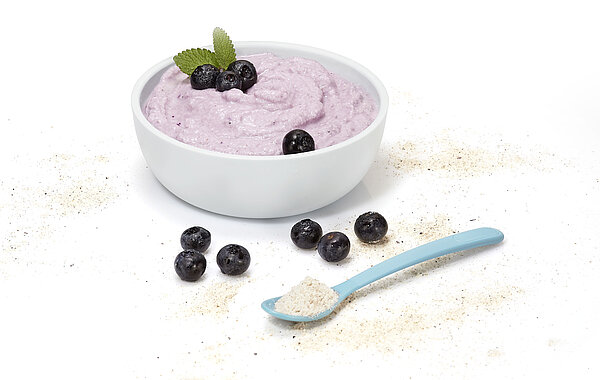
And yet: “Never change a running system” is not the best option in the face of growing challenges: powdered nutrition, just like pasty products or liquids, must not only be produced and filled hygienically, but also under increased cost pressure. In addition, as popularity grows, so does the variety of products and packaging. This means more frequent product changes and, as a result, more frequent cleaning of product-contact parts to prevent cross-contamination. Special attention has to be paid to the filling station and the filling heads.
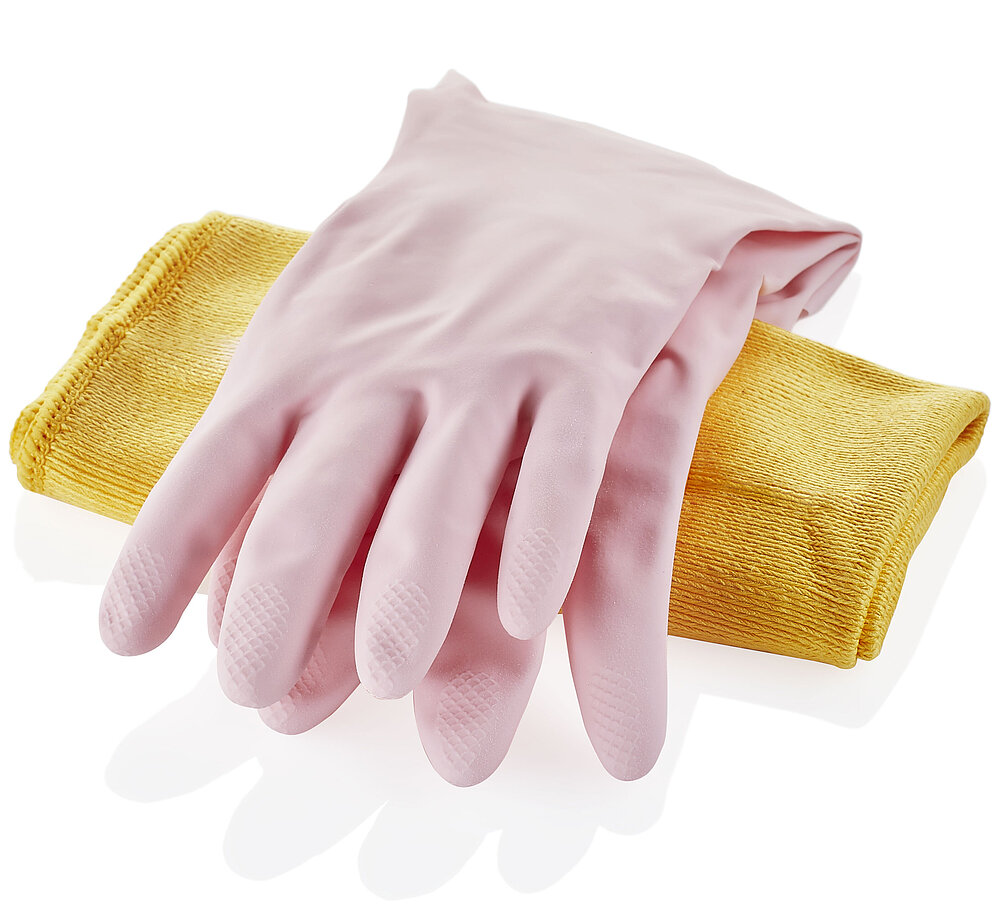
Manual versus Machine
In many cases, removed and disassembled components are still cleaned manually in a rinse room or cleaned dry with brushes and compressed air when changing batches. These manual processes are time consuming and labor intensive. And even after careful cleaning and visual inspection by experienced staff, there is a risk that residues will remain in hard-to-reach areas. In the case of dry cleaning, powder residues or contaminants, and in the case of wet cleaning, also moisture.
But how can cleaning cycles be shortened and system uptime increased? And how to ensure a repeatable, residue- and germfree cleaning result? Could industrial cleaning of the filling heads be the way to go? Preferably without disassembling them?
Clear, positive, and reliable answers to these questions were provided by the test cleanings at MAFAC for a global player in the food industry.
Process makes the Difference!
Although used to the highest demands and extensive specifications with dedicated requirements for machines and processes, this was a challenging task for the experts. The filling heads had to be hygienically clean and completely dry. Even in the feed channels and undercuts. The slightest residual moisture would encourage the growth of germs and impair the filling process. The powder could absorb moisture, agglomerate and clog the filling heads.
The test series was conducted at the Alpirsbach Customer Center on a MAFAC PALMA. With the two-bath system, MAFAC Vacuum Activated Purification (VAP) can be implemented to reliably meet cleanliness requirements up to High Purity. Various drying processes can also be integrated. Here, too, the MAFAC-typical rotation principle ensures optimized performance.
For the powder filling heads, impulse blowing, hot air and vacuum drying were combined in successive cycles. The result? Surprising to the customer's quality control staff. Surprisingly good, according to wipe tests and visual inspections after disassembly of the cleaned filling heads. All components – whether stainless steel, plastic or sealing materials – were completely free of residual moisture.
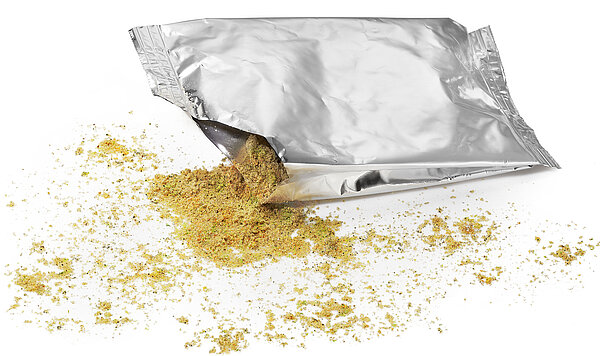
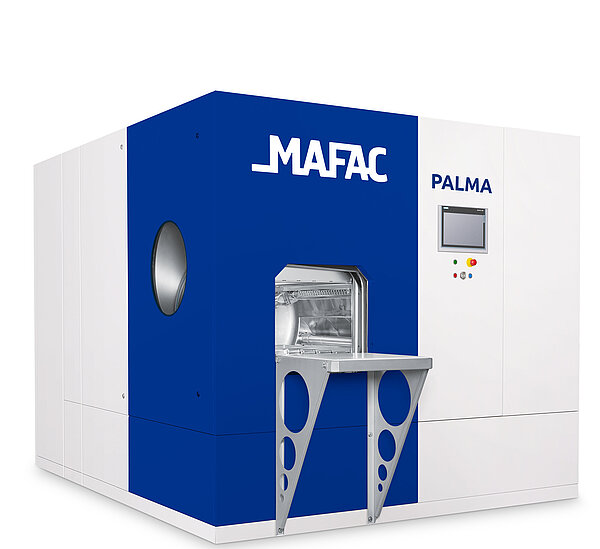
Convincing Efficency
As for efficiency, no questions remained regarding future investment: Manual cleaning takes approximately 30 minutes per filling head, meaning 25 hours for 50 heads. With the MAFAC PALMA and four filling heads per basket in a process that can be started at the touch of a button, it takes only 20 minutes, or just over four hours in total.
At the end of the test series, everyone involved was satisfied: MAFAC was able to prove that an industrial water-based cleaning process delivers best, reproducible results even with powdered foods and economic advantages compared to manual cleaning. On the customer side, the tests meant that the first major hurdle in the process change from manual to industrial was safely overcome, and quality assurance could give its “go” for an investment.