Perforated Plates for Surgical Baskets – clean without Residue and completely dry
Flexible, Validated, Standards-Compliant – Cleaning and Drying for Medical Components
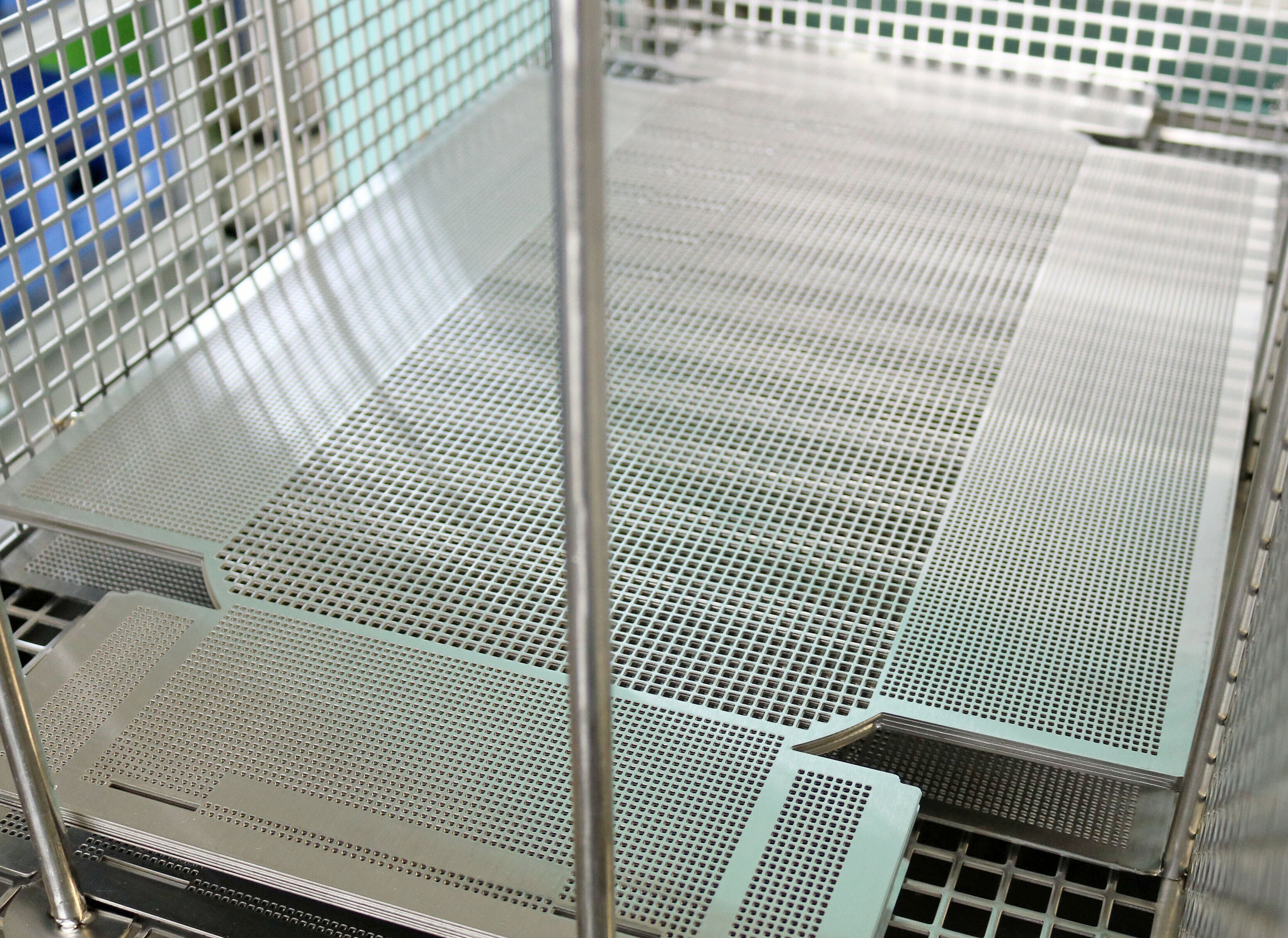
Both before handover to the next production step at MBengineering as well as before delivery to the customer, where they are given their final shape by metal forming and spot welding.
Therefore, the MAFAC PALMA plays an elementary role in the process chain, designed exactly to the specifications of the company with an individually dimensioned holding basket and a three-bath system.
“All instruments and technical aids used in the patient environment are subject to DIN EN ISO 9001 and the medical device standard ISO 13485. Achieving the required component cleanliness is a challenging task, especially for components in higher risk classes,” explains Martin Zepf, head of mechanical engineering at MBengineering and also responsible for quality management. Here special attention is paid to the quality of more than 5,000 stamped, forged, and formed parts for a wide range of medical technology products, manufactured daily in two-shift operation.
Highly sensitive Products and Processes
Surgical scissors, clamps, hooks, and tweezers: New manufacturing technologies and materials are improving the quality of components and end products. The catch? Not only medical products, but also manufacturing technologies are highly sensitive. For Martin Zepf and production manager Gianni Leocata, dirt residues carried over from one process step to the next are an absolute no-go. Residue-free, absolutely dry surfaces are a must.
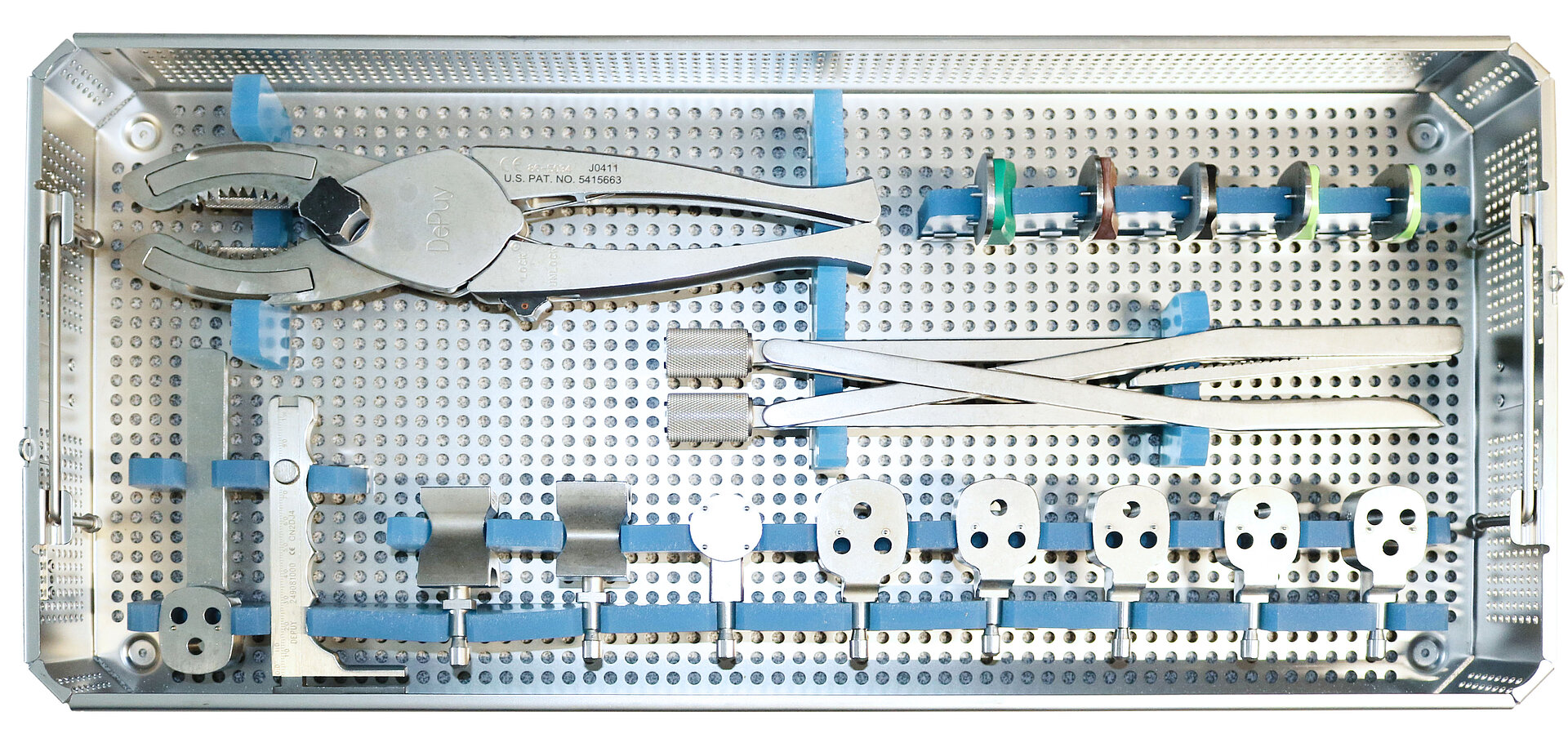
This key requirement was also stated in the requirements matrix for a new system to reliably clean stainless steel plates for surgical baskets from processing residues. The baskets are used to store, transport, and sterilize medical instruments. As Gianni Leocata explains, the punched blanks must therefore be “free of film and particulate contamination and completely dry to avoid contamination of our systems and to ensure the full functionality of the end products, for example through perfect welds.”
Further requirements: Cleaning and drying had to be economical and run in validated processes. The system also had to be flexible enough to be used for other workpieces and components and to be individually optimized for new specifications or more complex geometries. Finally, the blanks had to pass the EN ISO 10993-5 cytotoxicity test after final cleaning.
From the beginning, the company knew that cleaning had to be water-based and free of solvents to protect employees and the environment and to ensure the required biocompatibility of the products.
With the MAFAC PALMA, we are setting new standards for our customers and can clean different components significantly faster and with much higher quality. This benefits our internal production flow as well as the processes of our customers.
Martin Butsch, Founder and Managing Director
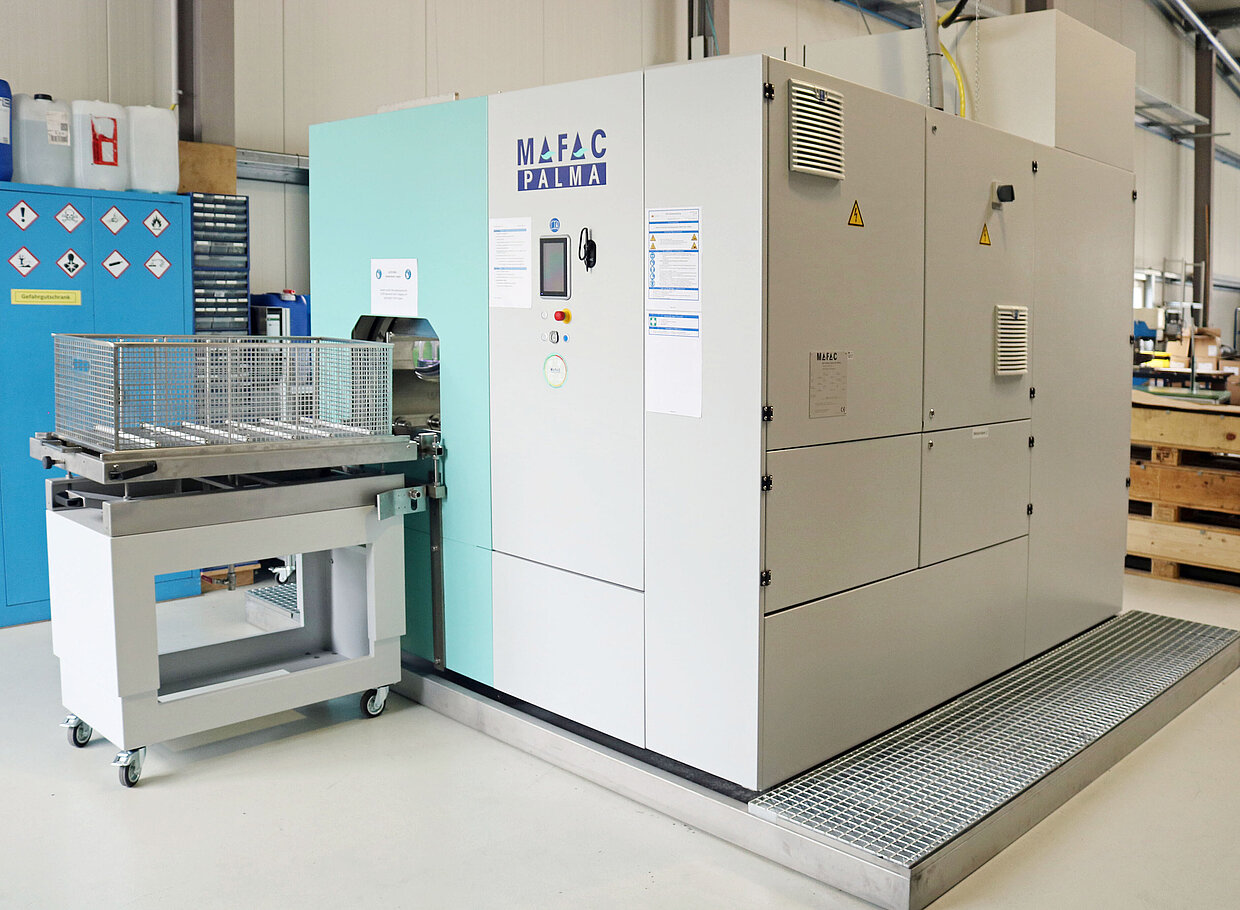
Done – with an individually configured MAFAC PALMA
Economical, validated, flexible, future-proof: With the MAFAC PALMA spray flood cleaning machine, Martin Zepf and Gianni Leocata were able to tick every box.
The MAFAC experts designed the basket receptacle system to allow several of the millimeter-thin, large-format perforated blanks to be cleaned and dried at the same time. The third holding tank ensures that the cleaning baths have a long bath life time despite the high oil input from the machining processes. "Thanks to the cascaded design, we only have to change the baths every three to four months at high capacity," concludes Martin Zepf.
The important thing for us is the high flexibility in the use of the machine. To get best results and being prepared for future challenging projects and cleaning tasks.“
Martin Zepf, Head of Mechanical Engineering
Multi-stage production, multi-stage cleaning and drying
From blank to finished product, the stainless steel plates undergo a multi-stage process of laser punching, straightening, grinding, and deburring. Cleaning is also done in two stages, with a short intermediate cleaning after laser punching and a 30-minute final cleaning after deburring. The blanks are exposed to a mild cleaning medium using the spray-flood method and then rinsed. The final cleaning is done in two phases – first from tank two, then from tank three. The drying process is also more extensive, with impulse blowing, hot air, and vacuum drying twice. With tightly packed batches, it takes about as long as cleaning.
This sounds time-consuming, but according to Martin Zepf, it is a clear advantage: “As with the cleaning process, the basket-nozzle-rotation in combination with the precisely set degree of drying ensures perfect results. In this way, we can prepare about 800 stainless steel blanks per shift for shipment.”
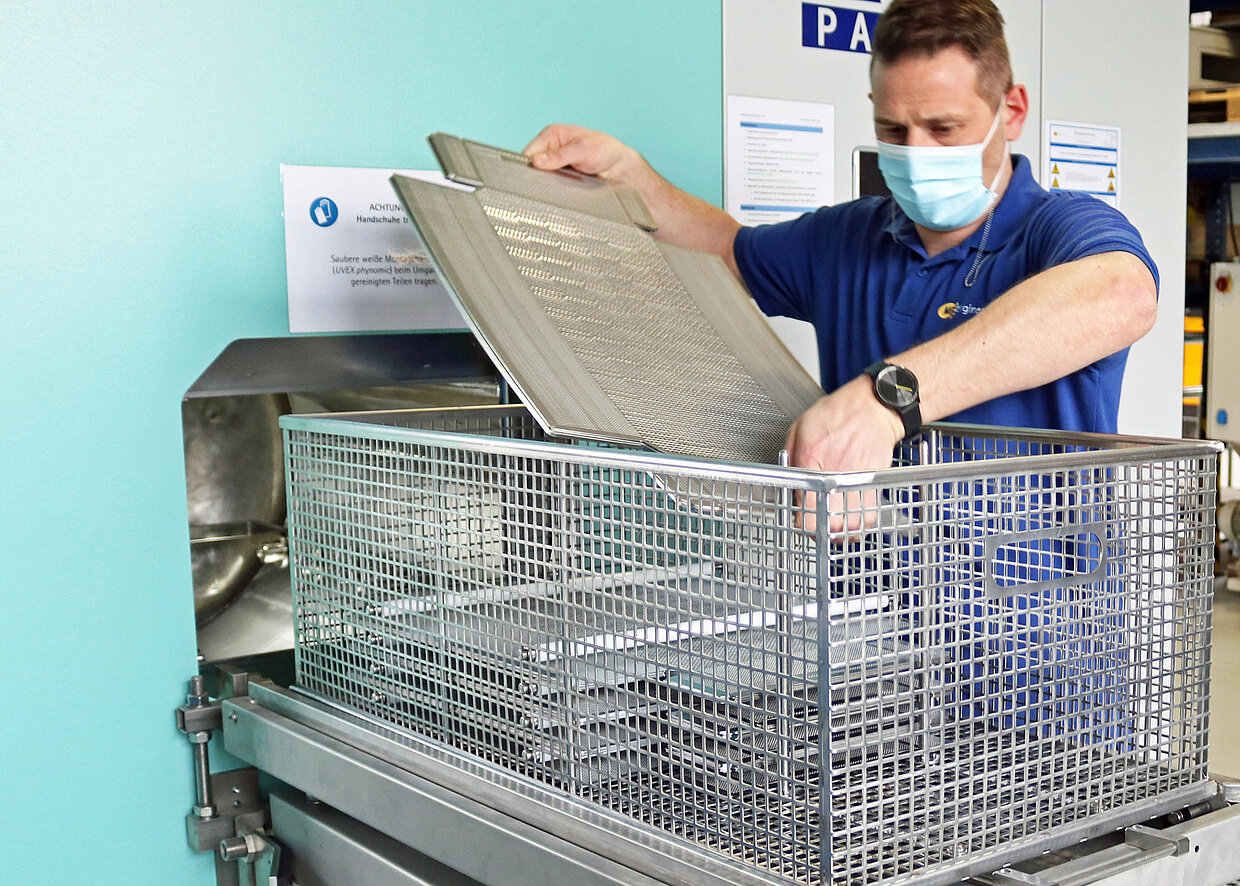
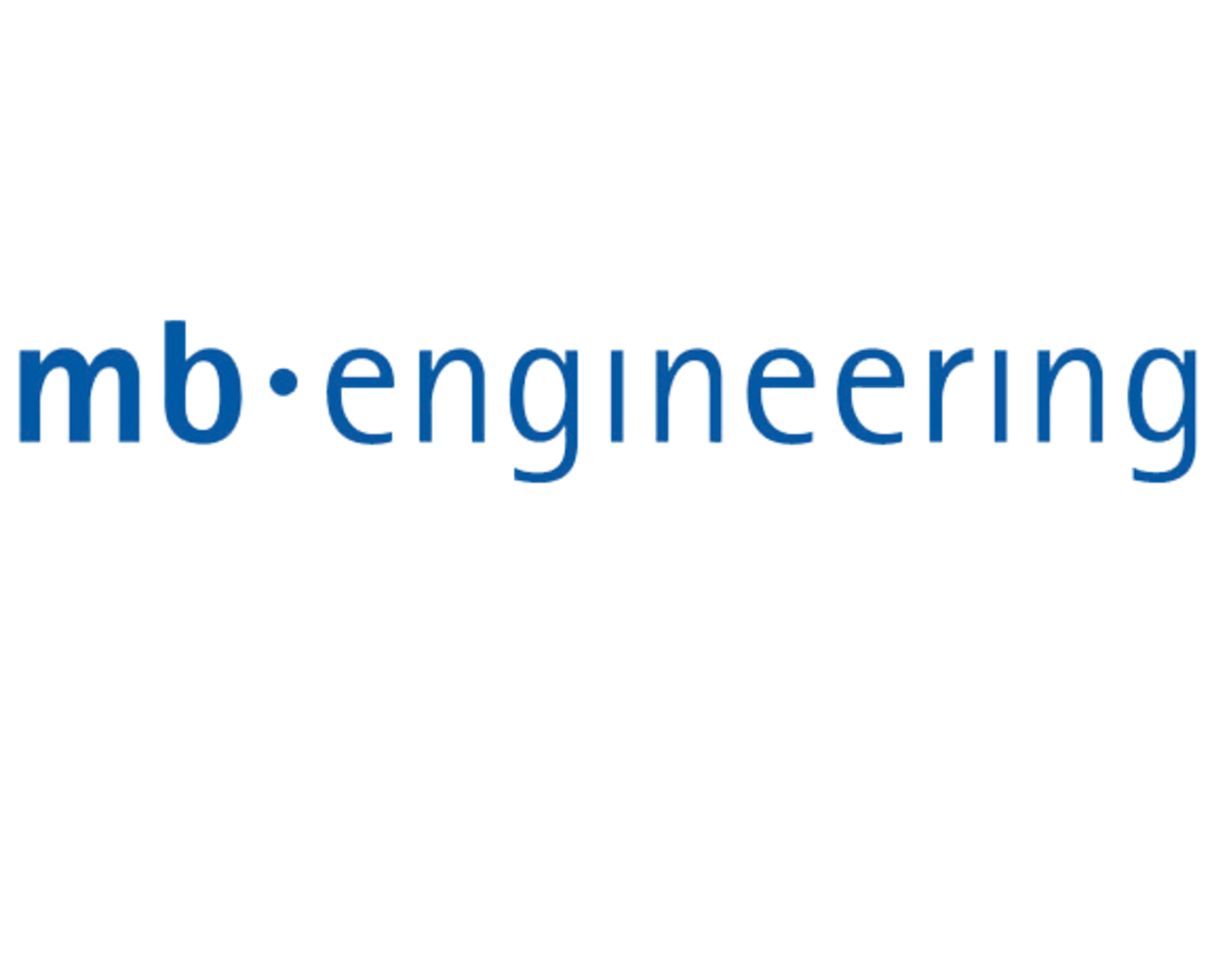
About MBengineering
Metalworking with laser cutting and punching, bending, and forming as well as water jet cutting for customers in the field of medical technology. Systems and processes for cleaning and processing plastics for mechanical and plant engineering. 3D data forging with non-contact measurement technology and data acquisition, spare parts design, and additive manufacturing: MBengineering GmbH & Co. KG offers a comprehensive portfolio with a high degree of vertical integration.
The company, based in Dürbheim near Tuttlingen, is one of the leading manufacturing companies in southern Germany and employs around 40 people.
MBengineering GmbH & Co. KG | 78589 Dürbheim | Germany