An exceptional Specification
Precision Engineering: when Component Cleaning meets the highest Standards
Precision from the Swiss Jura
Traveling from Neuchâtel, on the lake of the same name, into the mountains, one naturally remains in the here and now. And yet one comes to places where time loses its meaning. For here in Le Locle and La Chaux-de-Fond, watchmaking is as highly valued as it was in 1850, when Constant Othenin-Girard opened his watchmaker's workshop.
On the other hand, time has a special meaning in the region:
The “Top 6” of the world's most famous luxury watch brands are located here. Using innumerable components, they produce watches in the finest tradition of craftsmanship that are both collector's items for the wrist and first-class investments. And just as the buyers of these watches expect more than just a precise time display, the manufacturers also expect more than usual from their supply partners.
Designing a ready-to-use process down to the last detail and then getting a commitment to buy the machine? We see this as a leap of faith and are pleased that our expertise is increasingly in demand in this particular market segment.”
Thomas Gutmann, Head of Customer Support at MAFAC
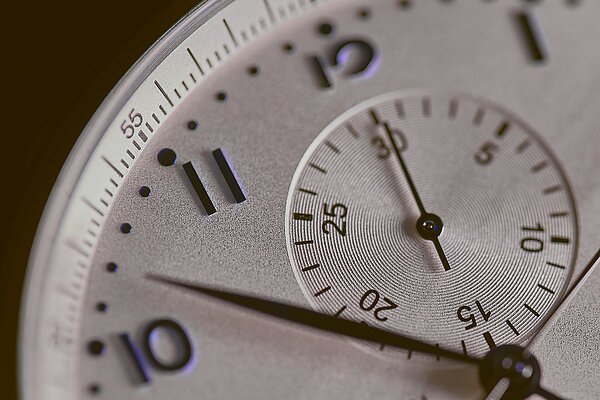
High Expectations of the Process Partner
Whether it is a machining center for manufacturing the finest parts or a cleaning system to remove traces of processing from visible watchmaking components after polishing the high-performance steel:
The specifications are always “extraordinaire“ and have to be met precisely – in advance.
What is needed, is a process solution that runs smoothly right from the start.
Thomas Gutmann, Head of Customer Support at MAFAC, points out:
“Customers from the watch and jewelry sector, but also from medical technology, want to see this solution in live operation. Not on one of our systems in the MAFAC Customer Center, not in a test cleaning. But on their project machine, with their original parts.”
This means that not only the FAT takes place at the machine manufacturer, but also the Site Acceptance Test, usually performed at the customer. During the procedure, the system is verified for function and completeness of the characteristics defined in the specifications. The process parameters are fine-tuned prior to installation.
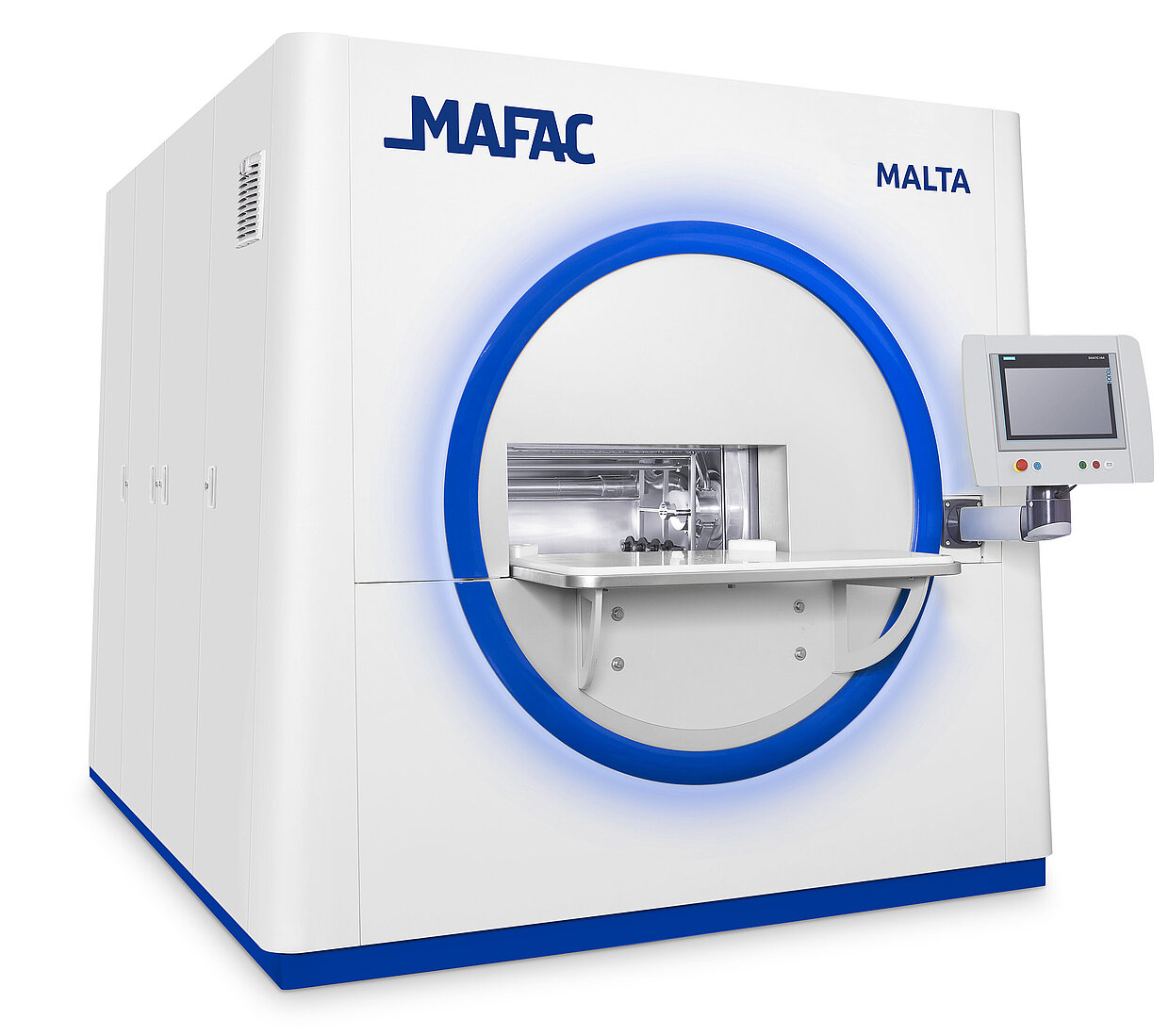
A Leap of Faith – received and safely redeemed
For a partner like MAFAC, this means going the extra mile.
Designing and building a cleaning machine – a MALTA for the watch brand from La-Chaux-de-Fonds – according to the specifications. Developing the cleaning and drying process, selecting and fine-tuning the cleaning medium, carrying out tests and optimizing it to such an extent that every point in the “Cahier des charges” is ticked off and the system can be sold. A risk? According to Thomas Gutmann, much more “a leap of faith. We are proud of this, and pleased that our expertise is increasingly in demand in this particular market segment.”
But why a cleaning machine from the Black Forest for Haut-Jura? Because the customer's representatives found exactly what they were looking for: the MALTA, the right system for cleaning high quality watch components after grinding and polishing and drying them absolutely stain-free. And with MAFAC, the right partner for a customized process solution.
Special Requirements, special Solutions
As is typical for MAFAC, the parts are cleaned with motion, with mechanical pulse exchange. But unlike other applications, the pressure is significantly lower.
For comparison: Automotive components are cleaned at a pressure of 15 bar. Such turbulence and force would be counterproductive for the fine, highly polished elements. The application department in Alpirsbach therefore carried out various tests and finally designed the cleaning process with a pressure of just 0.5 bar.
As a result, says Thomas Gutmann, “the process takes considerably longer. However, in view of the many months it takes to produce a watch of this type, this is of no consequence. Time plays no role here, even with multi-stage targeted drying. It's all about achieving the best possible quality.“