No Reason for Worry Lines!
Solvent-free Cleaning in the Cosmetics Industry
Safe and clean: Cosmetic GMP
Ingredients that provide hours of radiance on the skin or color on the lips cannot be removed from the face by water alone, nor from components in filling systems. And yet, water-based cleaning is a must in the cosmetics industry. On the one hand, to ensure the safety of employees, to protect consumers from solvent residues, and to meet the standards of DIN EN ISO 22716 – Cosmetics – Good Manufacturing Practice (GMP). On the other hand, to reduce the ecological footprint and obtain appropriate certification for environmentally friendly cosmetics.
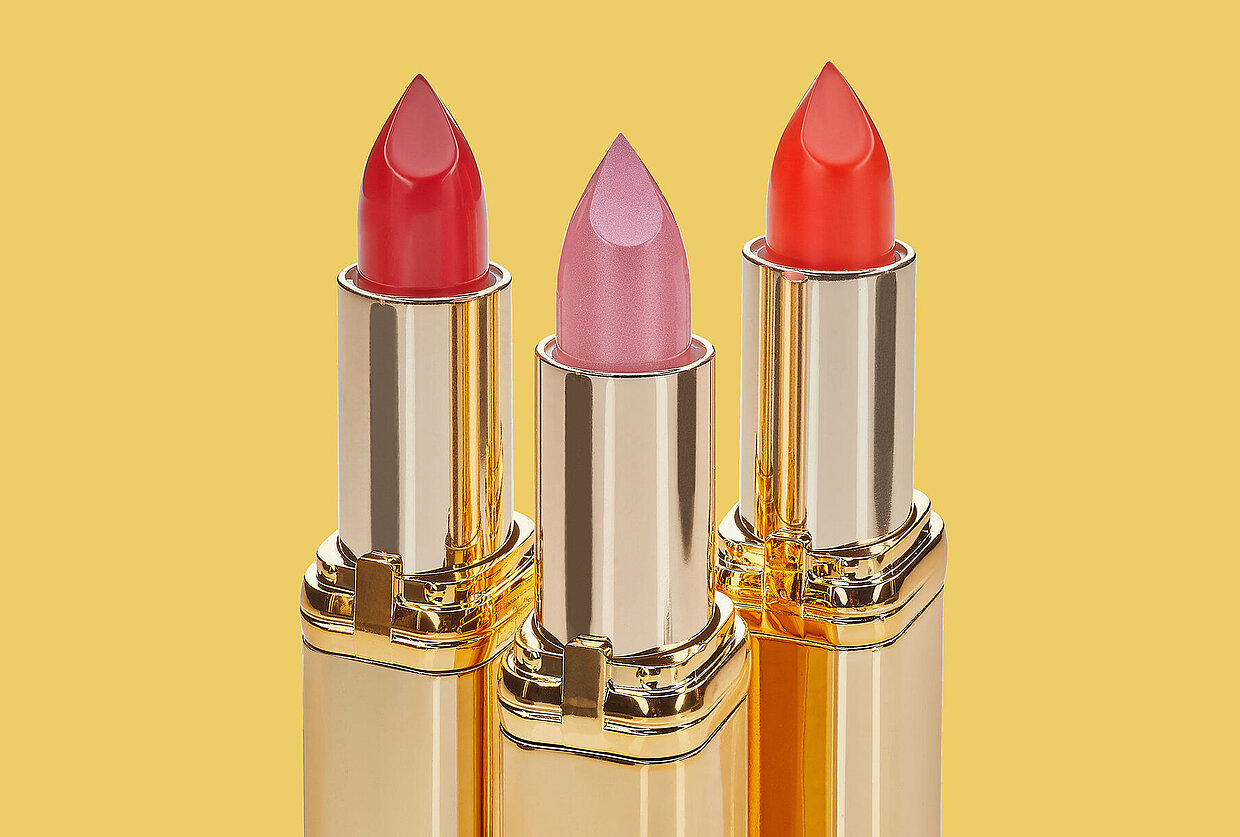
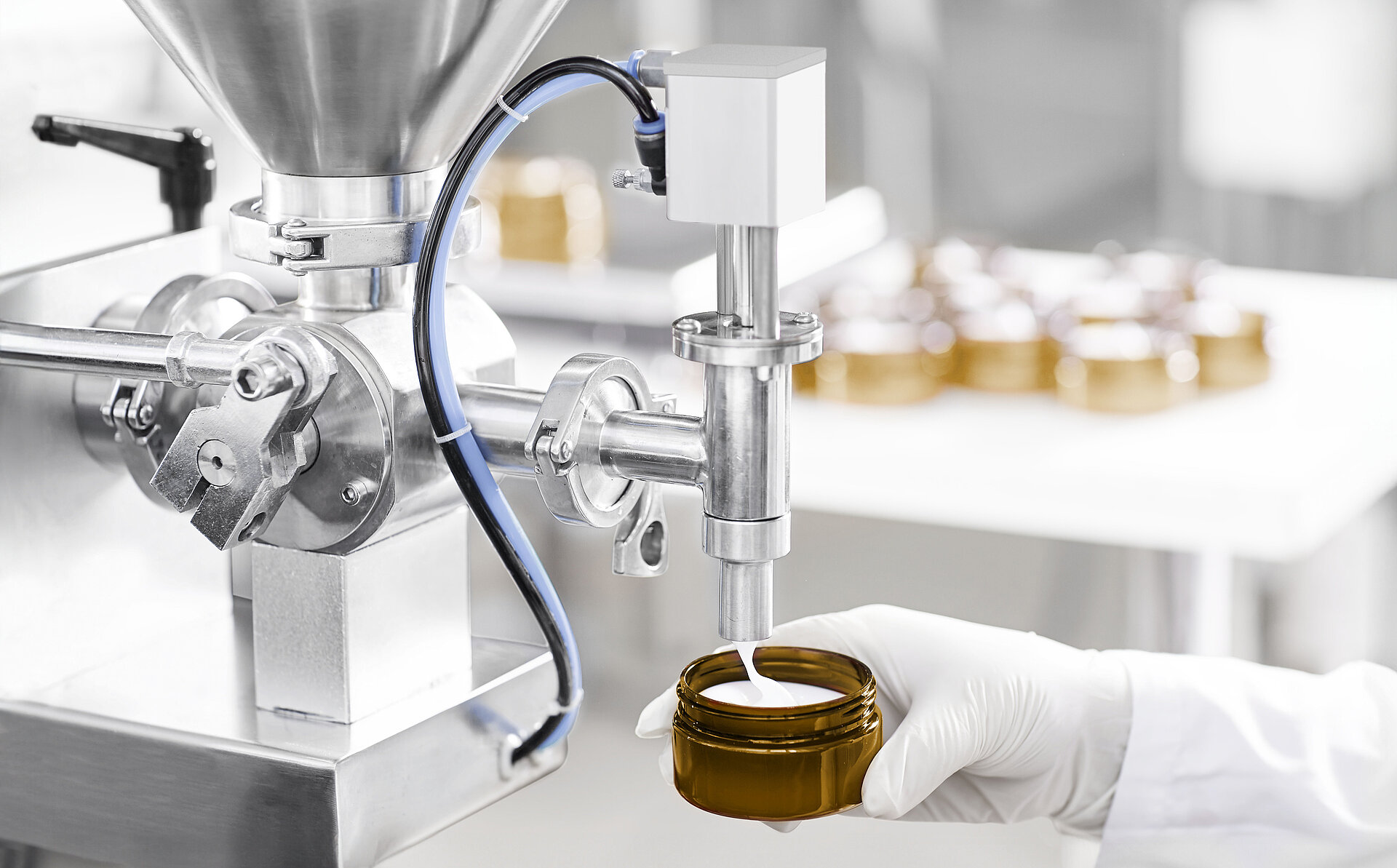
Common Processes – safe Options?
When cleaning product contact parts, many manufacturers still rely on the following water-based processes: Immersion cleaning, COP cleaning, or purely manual soil removal. Immersion cleaning involves placing equipment in a solution of water and detergent, with a stirrer providing some mechanical action.
However, this is not sufficient to dissolve persistent contamination.
Therefore, detergent is dosed at higher rates, or the equipment must be cleaned repeatedly in a time-consuming manual process.
COP – Clean out of Place – is another option. Here, parts are also disassembled, and residues are removed using high-pressure equipment.
The performance is highly operator-dependent, and the temperature is often too low to protect staff. The same applies to manual cleaning:
Again, the temperature limits the effect, and the process is time-consuming and labor-intensive.
It is almost impossible to achieve a consistent result, and operators often follow the "much helps much" principle, processing components too much or applying too much detergent.
What's more, complex formulations mean that there are many different types of contamination.
These push the above-mentioned processes to their limits. If a lipstick is long-lasting, it will also be water-repellent, and persistent oily layers will form on the filling equipment.
If a tinted day cream has a high pigment content, it will look good on the skin. Still, the iron oxide leaves a thin powder coating on the part's surface, which is also difficult to remove.
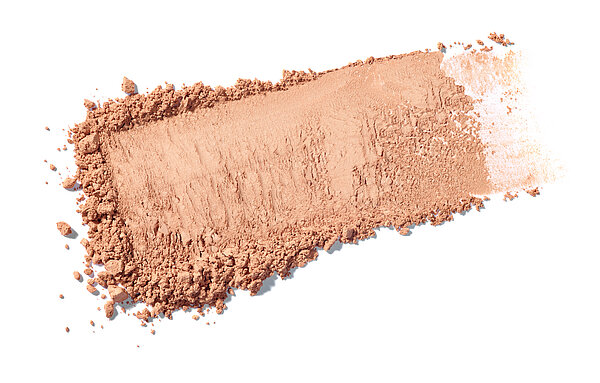
Buckets full of Challenges
Too many variables to guarantee a reliable process:
This was also the opinion of the production managers at the french site of an international cosmetics company, who asked MAFAC to carry out a series of tests.
The aim was to remove the very different types of contamination in continuous cleaning processes on a single system without leaving any residue.
If the tests were successful, the company would invest in a machine and move from manual to mechanical cleaning.
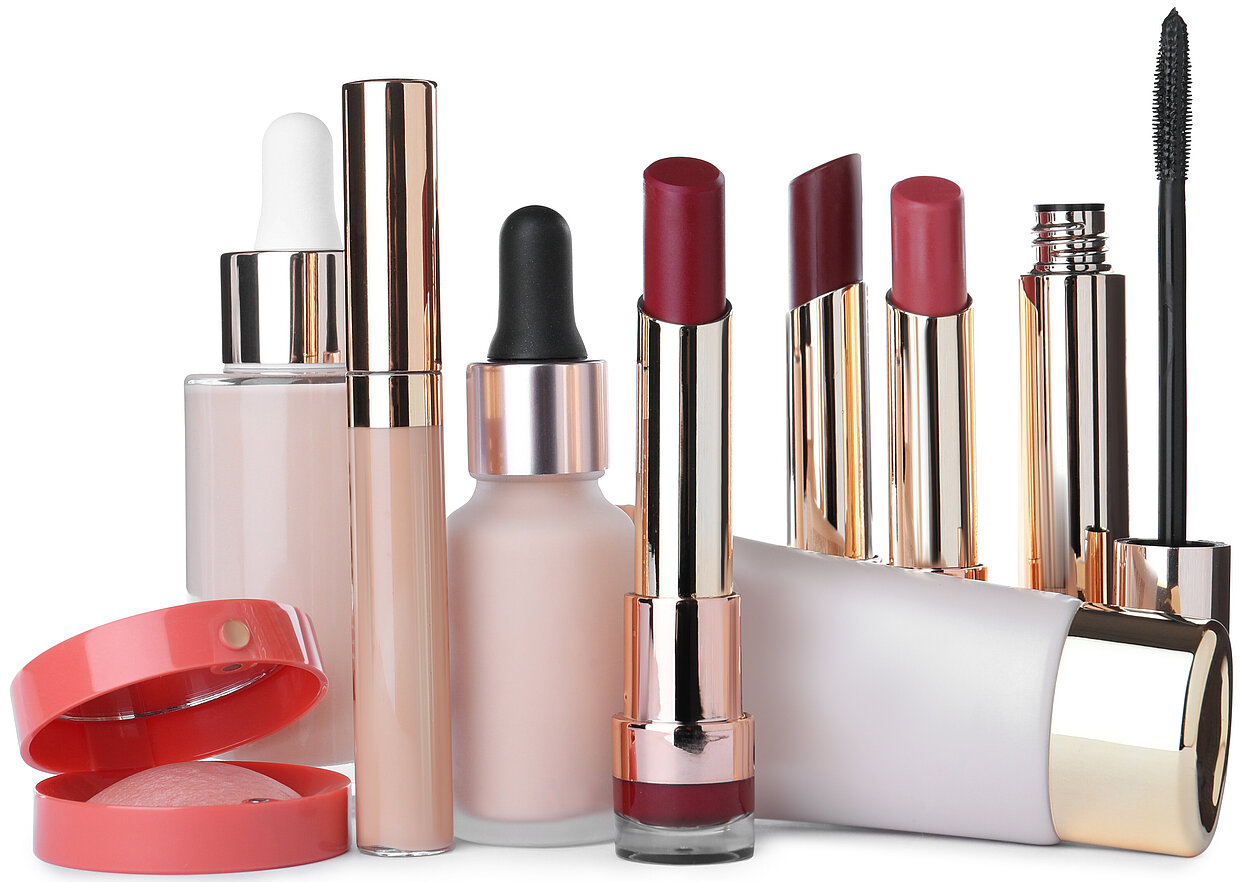
To perform the tests, the manufacturer sent pallets of 10-liter containers to Alpirsbach with the products ready for filling: Makeup, creams, suntan lotions, shampoos. In addition, various parts from the filling systems: valves, fittings, pipes, supply lines, seals, filling heads, and much more.
The tests made clear how efficient water-based cleaning is with our patented technology of simultaneous rotation of basket and spray system, and how precisely the various parameters can be set to safely remove a wide range of contaminations. Meanwhile with MAFAC Vektorkinematics and MAFAC VAP, we provide our customers further innovative technologies specifically designed for demanding cleaning routines in sensitive industries.“
Dipl. Ing. Tobias Lutz, MAFAC Application Engineer
Clean and sterilized by high Temperatures
The cleaning process should only involve the already certified detergents that are also used for manual cleaning.
Environmentally friendly surfactants in low concentrations, specifically tailored to the high standards of cosmetics production.
More specifications: The cycle time per batch had to be a maximum of 45 minutes to make product changes faster and more economical.
Plus: The system had to be designed as a three-bath system. Media tank one for cleaning and media tank two for rinsing. Finally, media tank three for rinsing at 85°- 90°C to ensure sterility.
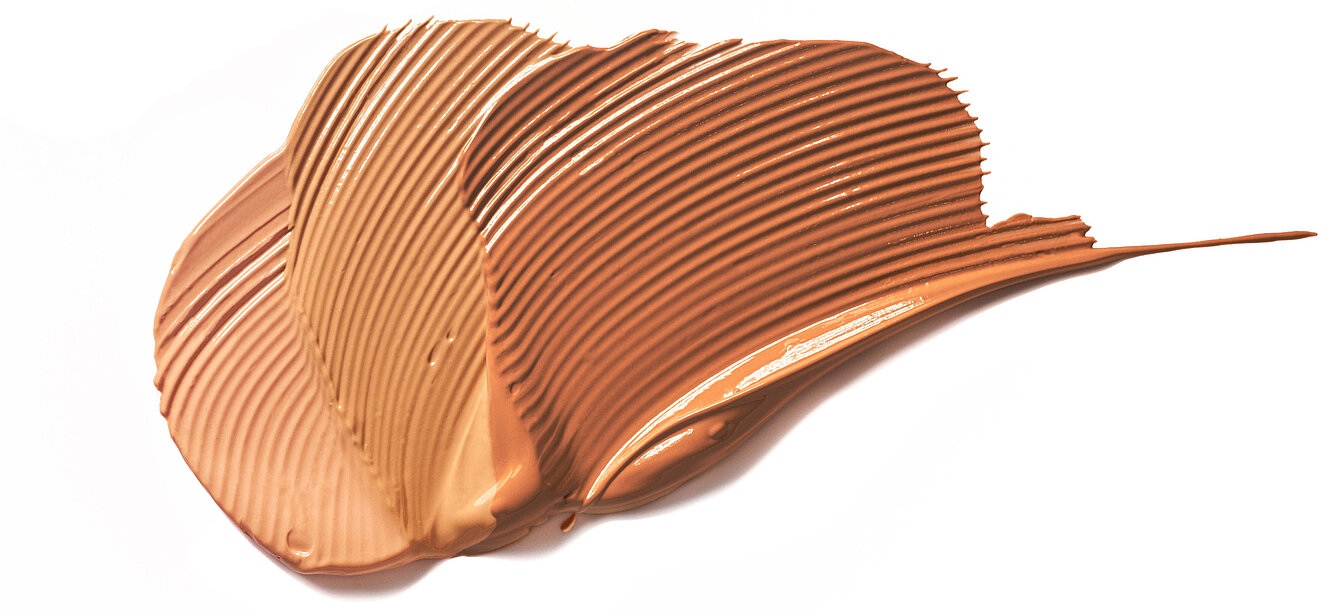
A test series with an unusual start: Cream up everything first
Given the specifications – maximum 45 minutes, three baths, complex geometries, high cleanliness – the application technology department decided to run the tests on a MAFAC PALMA spray-flood system.
And to use ultra sonic as an added-on process.
In order to develop the best program for each product, the equipment was thoroughly “creamed up” and then cleaned. This was done until the ideal combination of dynamic movement, temperature, time and water/additive combination was achieved.
For water-soluble products, the programs were provided very quickly.
The parts were completely clean in an average of 30 minutes.
Especially waterproof makeup proved to be particularly persistent.
Wipe tests initially left slight flimic contamination on the inner contours.
What to do? Adjust one of the parameters mentioned before. In this case: Time.
The cleaning process was extended to about 10 minutes, which, in combination with the rotation of the basket and spray system, reliably removed even the last residues.
Last but not Least: Shampoo
Another challenge: Shampoo. The product-carrying parts were easy to clean, but the shampoo residue caused heavy foaming in media tank one. The addition of defoamer was out of the question, as this element would be “alien” to the process and therefore undesired by the customer for consumer protection reasons.
But too, this last difficult task could be successfully solved:
Based on gained experiences and former approaches to handle foaming products, several constructive adjustments were made to prevent foam intruding the cleaning chamber.
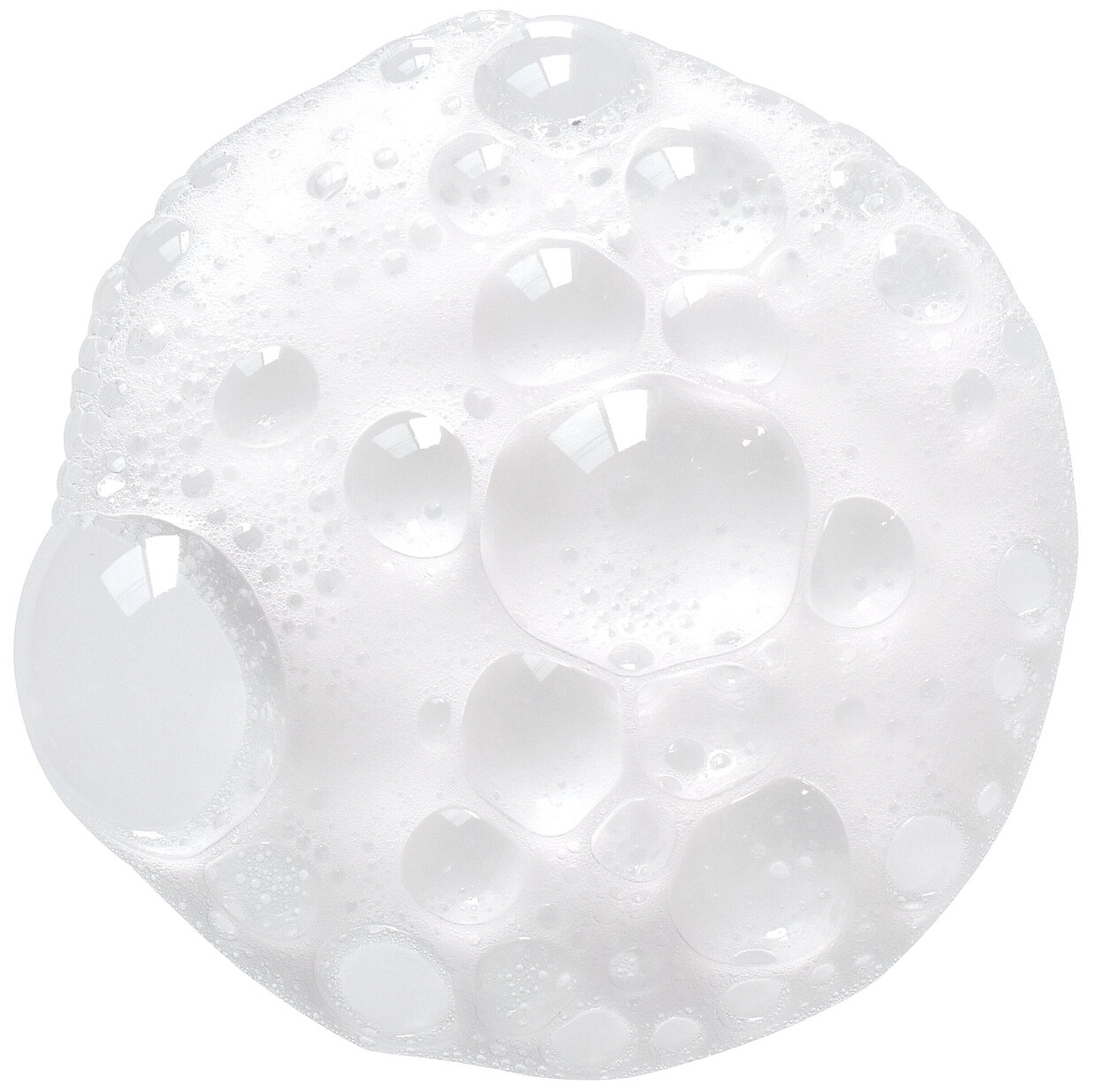
Expectations more than met!
The customer, who was on site several times during the tests, concluded:
All challenges were more than met! In most cases the cycle time was well below the maximum 45 minutes and even stubborn residues were safely removed.
And with the MAFAC PALMA, not only the right system was found, but also future optimized cleaning in safe processes guaranteed. Bought!
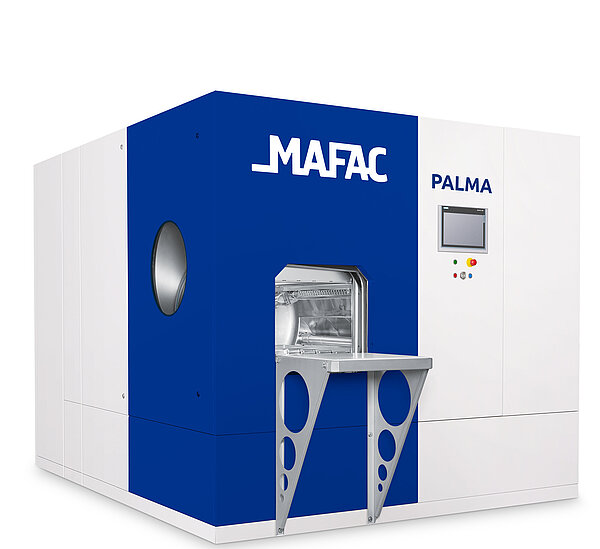
MAFAC PALMA with 3 Baths
The test and later customer system was designed as a three-bath unit using MAFAC Kinematics and ultrasonics.
Today, MAFAC offers further innovative technologies specially developed for highly sensitive industries and applications.