Removing Oxides – with water-based Cleaning
Oxide Removal and Corrosion Protection – All in the Cleaning Process
Cleaning – a Key Process
Whether fluid components for the automotive industry, milled or turned parts, valves, control blocks, hubs, gears or products for injection technology, cleaning plays an important role in TEM deburring. Oil, grease and coolant residues must be removed beforehand, as well as the oxide layer that forms after deburring. This can impair subsequent production steps such as coating, painting, welding or soldering, and thus the functionality of the products. Absolute absence from burrs is a must, especially for applications under hydraulic pneumatic conditions.
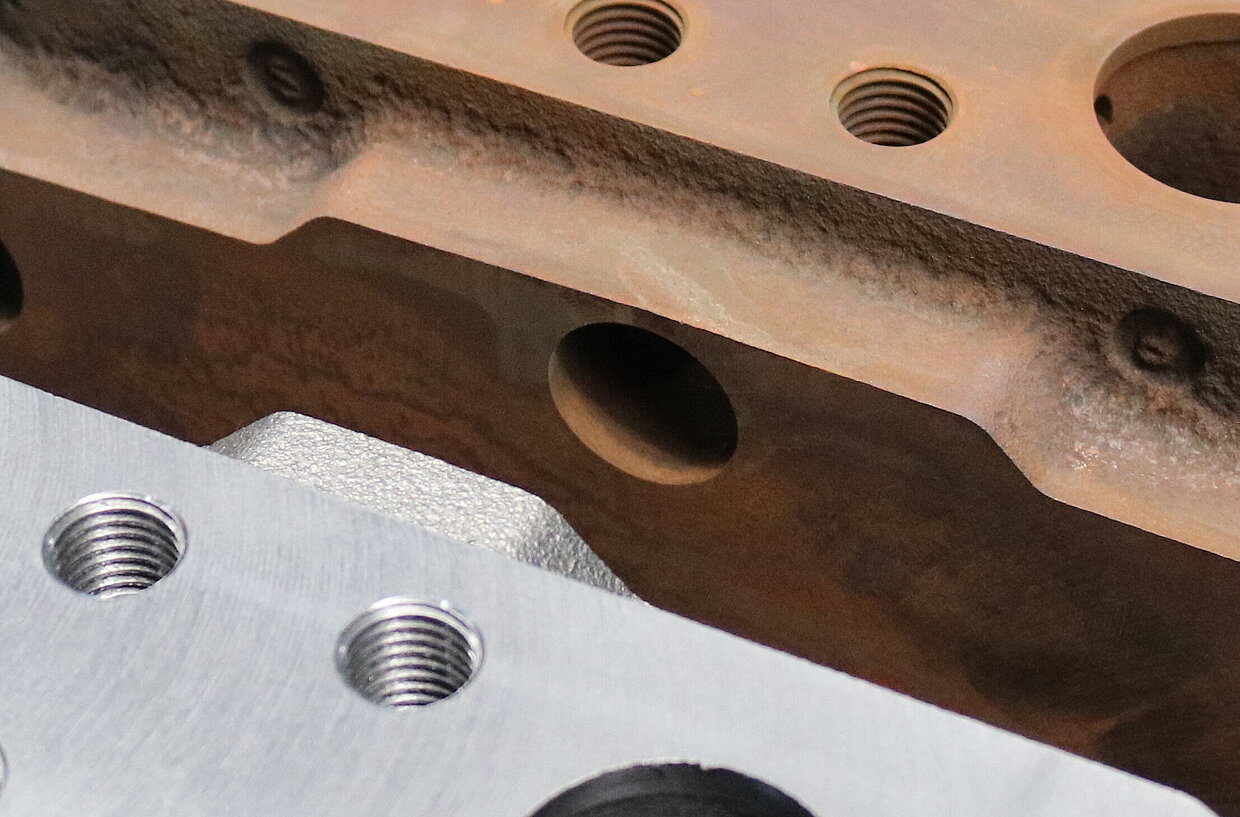
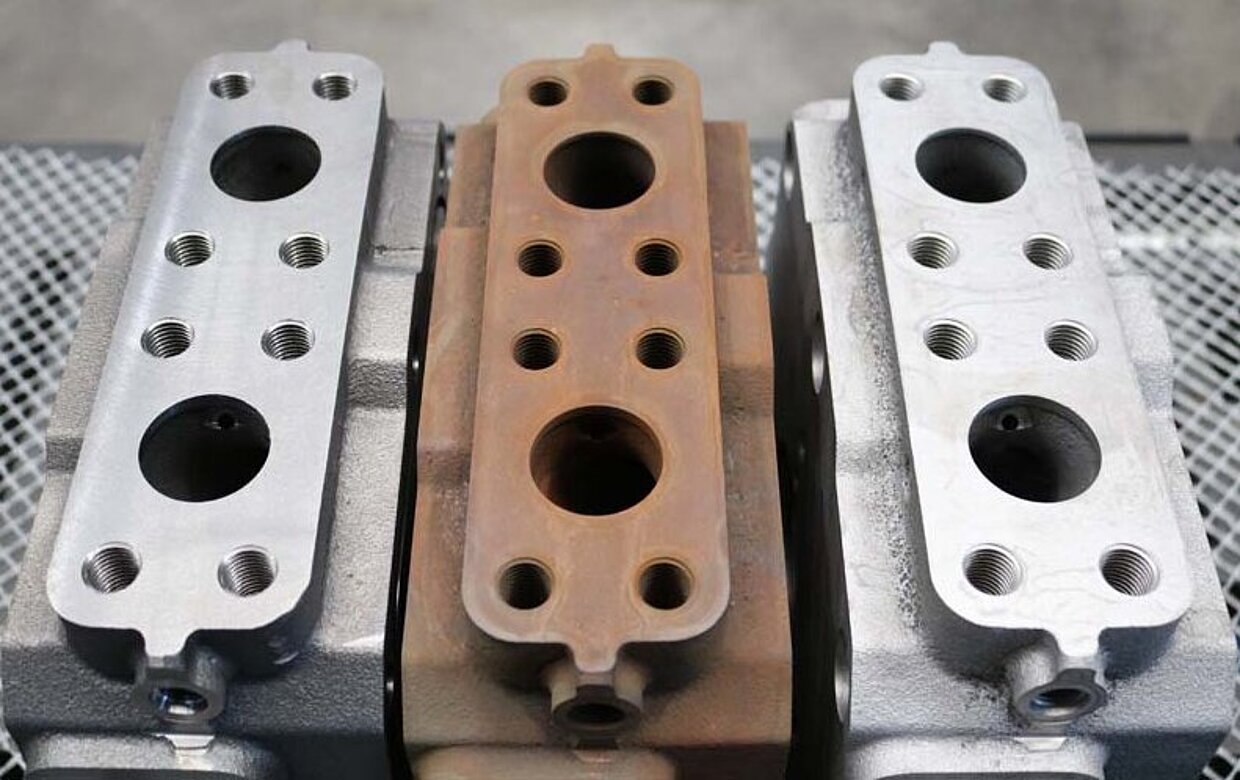
The oxide layer varies depending on the material: on steel and gray cast iron workpieces, reddish-brown to black-brown rust forms, partly adherent and partly loose as soot-like dust. Oxide and graphite are deposited deep into the pores of the rough surfaces of cast parts. On aluminum components, oxide develops in the form of stubborn stains and streaks.
Despite the differences in material behavior, the requirements for parts cleaning are equally challenging:
Cleaning must be gentle and effective, and surfaces must be well protected against corrosion.
Residue-free Cleaning – water-based
MAFAC systems enhance the effect of the cleaning medium – water plus detergent– through a patented kinematic process principle. This combination leads to very good results when cleaning strongly adhering oxide layers. During the wet phase, turbulence is created by co- or counter-rotation of the basket holder and spray system. This turbulence, in combination with temperature, detergent and time, ensures a safe and effective cleaning effect.
For demanding cleaning after TEM deburring, a three-stage process is recommended in which spraying and flooding processes alternate. A neutral deruster is added to tank one, an additive for post-cleaning to tank two, and the final rinsing process with corrosion protection takes place in tank three. The choice of neutral detergent depends on the material; the pH can be precisely adjusted by adding additives: For steel, a product with a slightly acidic pH is used; for aluminum, a product with a more acidic pH (pH 2-4, organic acid) is applied.
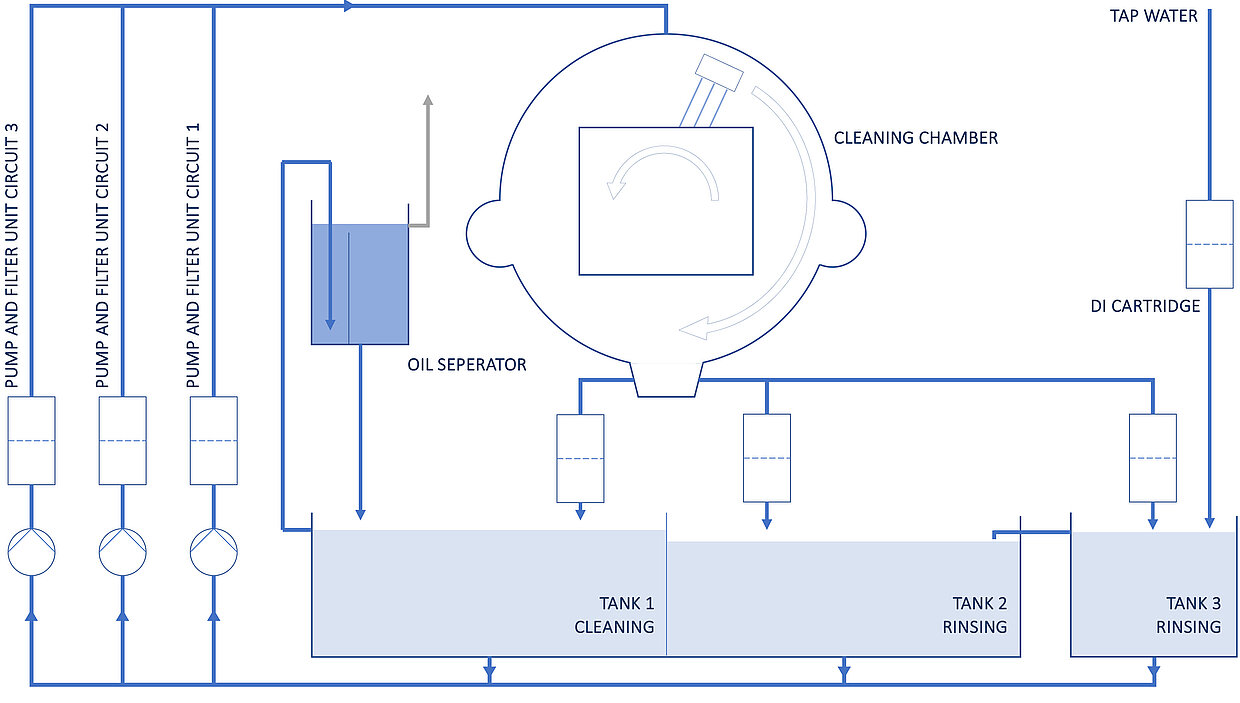
All neutral derusters are gentle on the material, user-friendly and can be combined with suitable surfactants for better wetting of the component surface. In addition, there is no hydrogen embrittlement, which can lead to component failure.
The advantages of the three-stage cleaning process are particularly evident with gray cast iron. In phase one, oxides are removed using a combination of spray and flood cleaning, often combined with ultrasound. In phase two, the highly active component surface is immediately neutralized by the addition of an alkaline cleaner. Ultrasound provides a post-cleaning effect. In phase three, the temporary corrosion protection is applied.
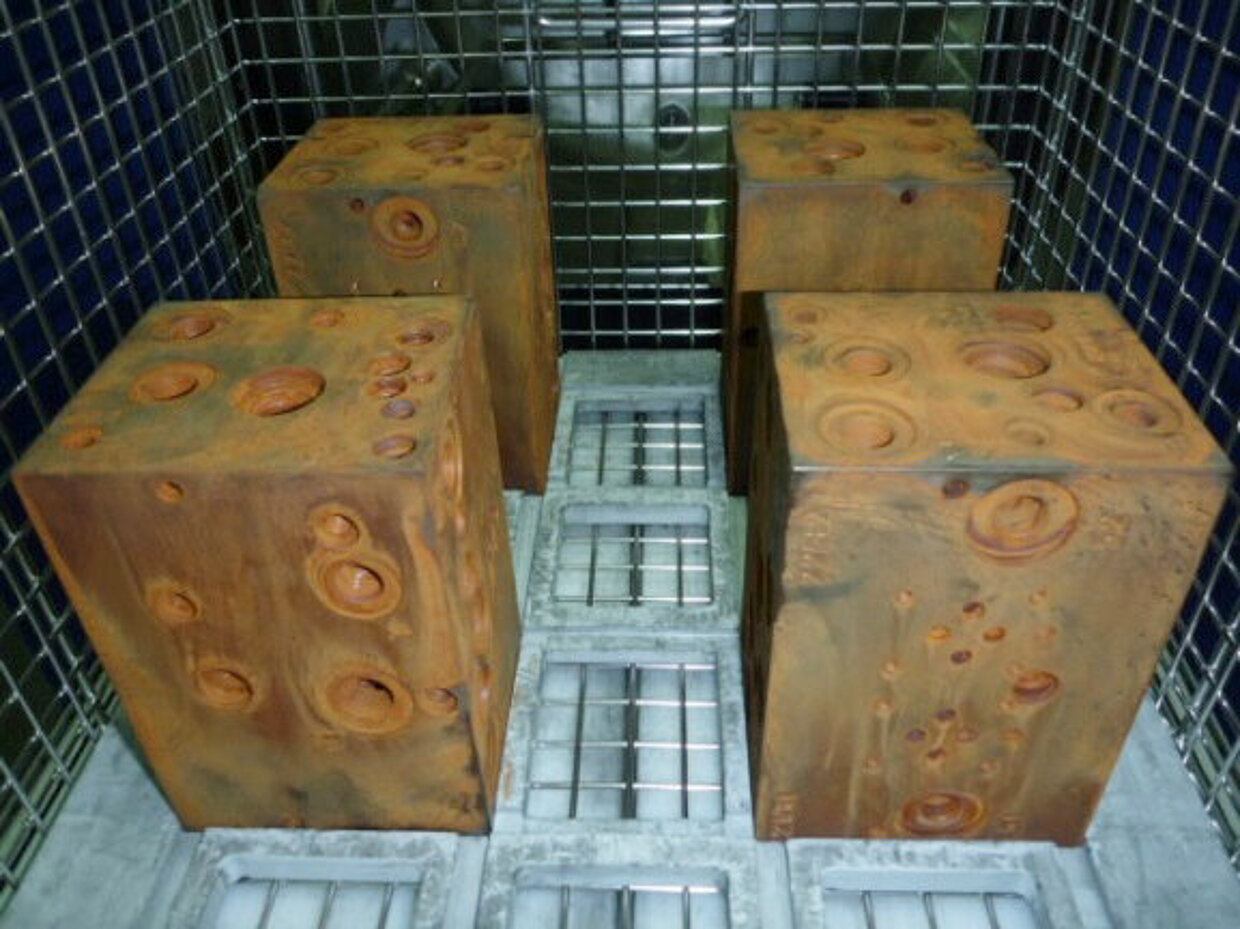
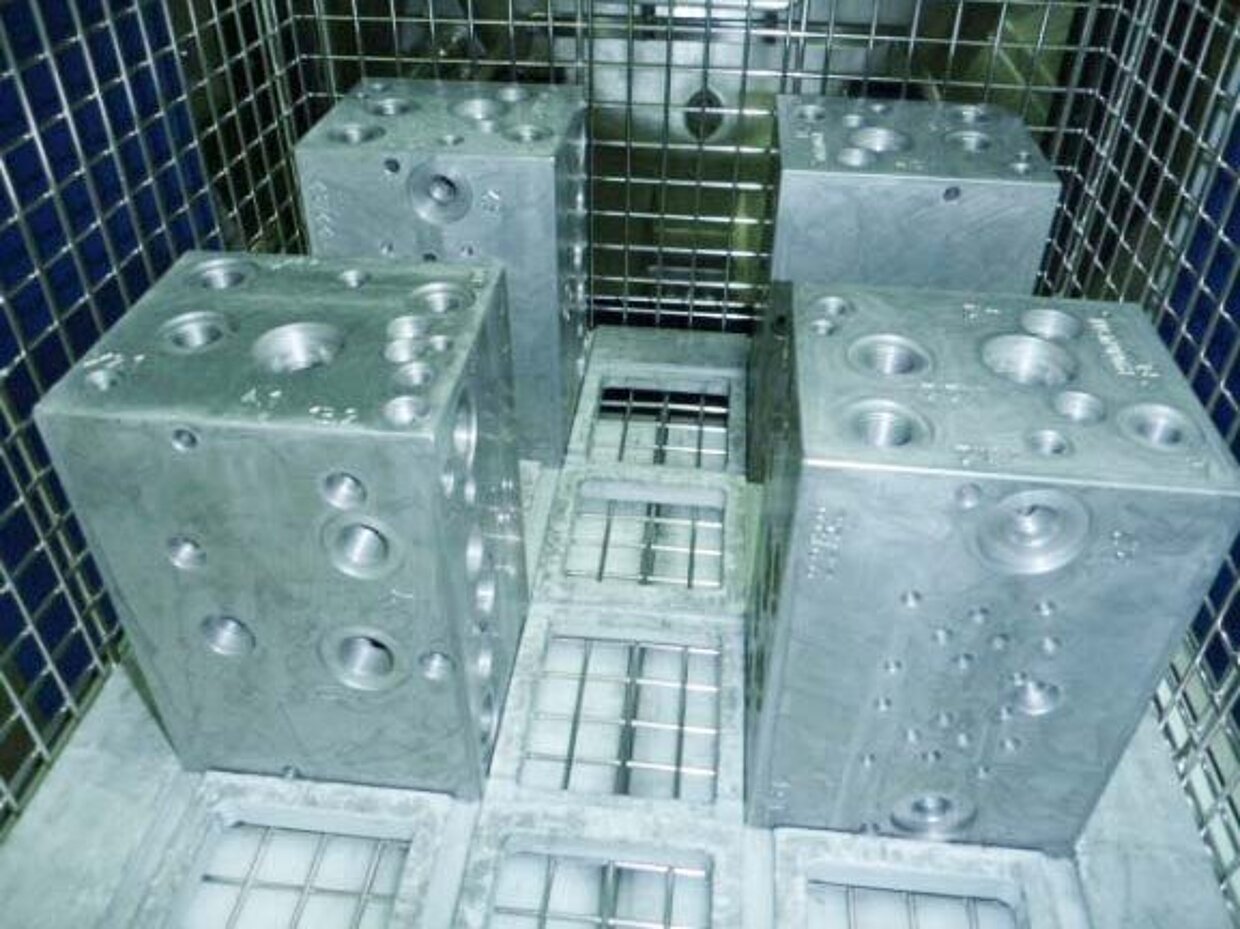
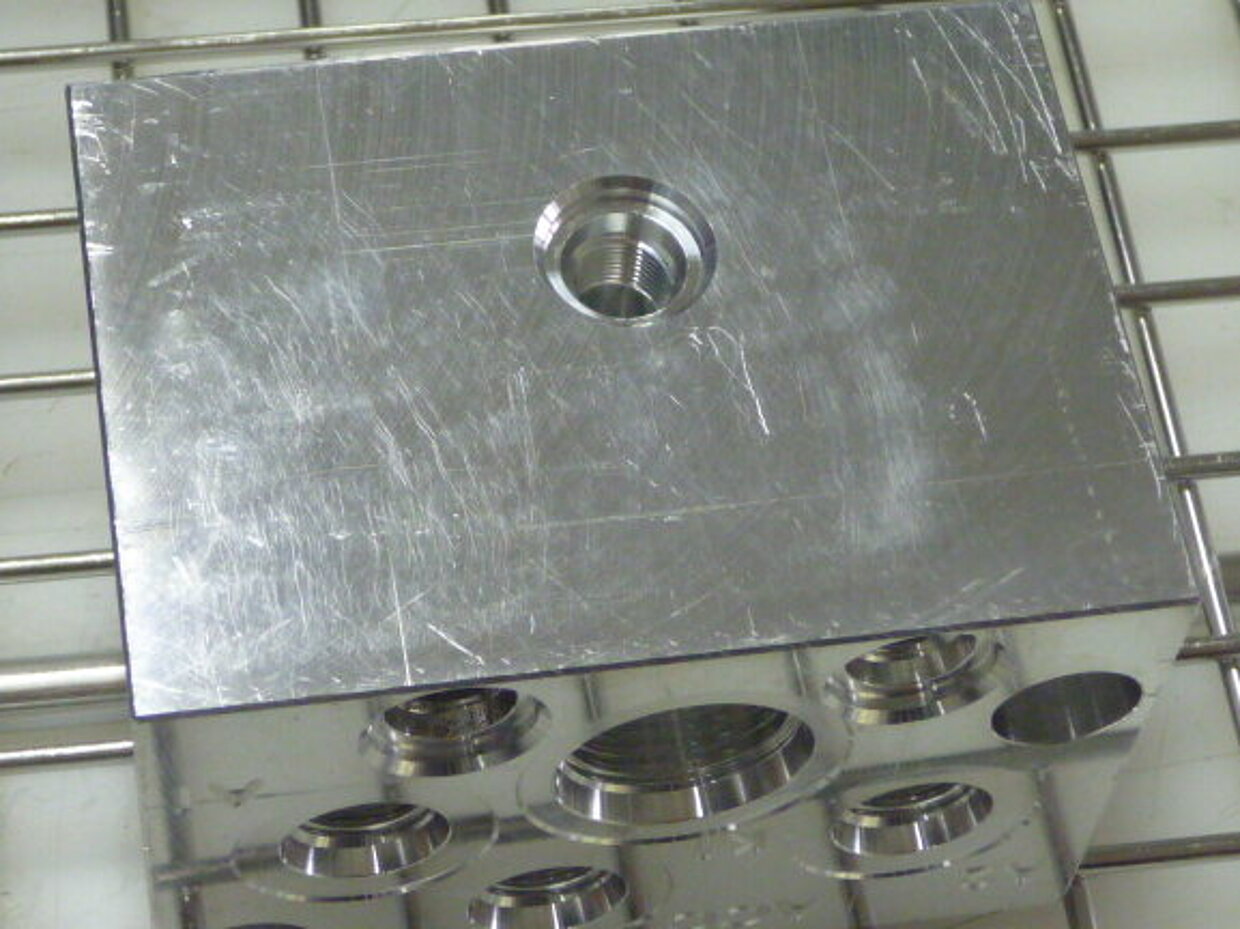
Economical – and Resource-efficient
The combination of kinematic process technology and a three-bath system not only makes sense in terms of precisely adjustable cleanliness, but also reduces the need for cleaning additives by up to 15 percent compared to other processes. This not only simplifies bath changes, but also saves costs for these additives and energy. In addition, bath life is increased because there is significantly less carryover between tanks two and three.
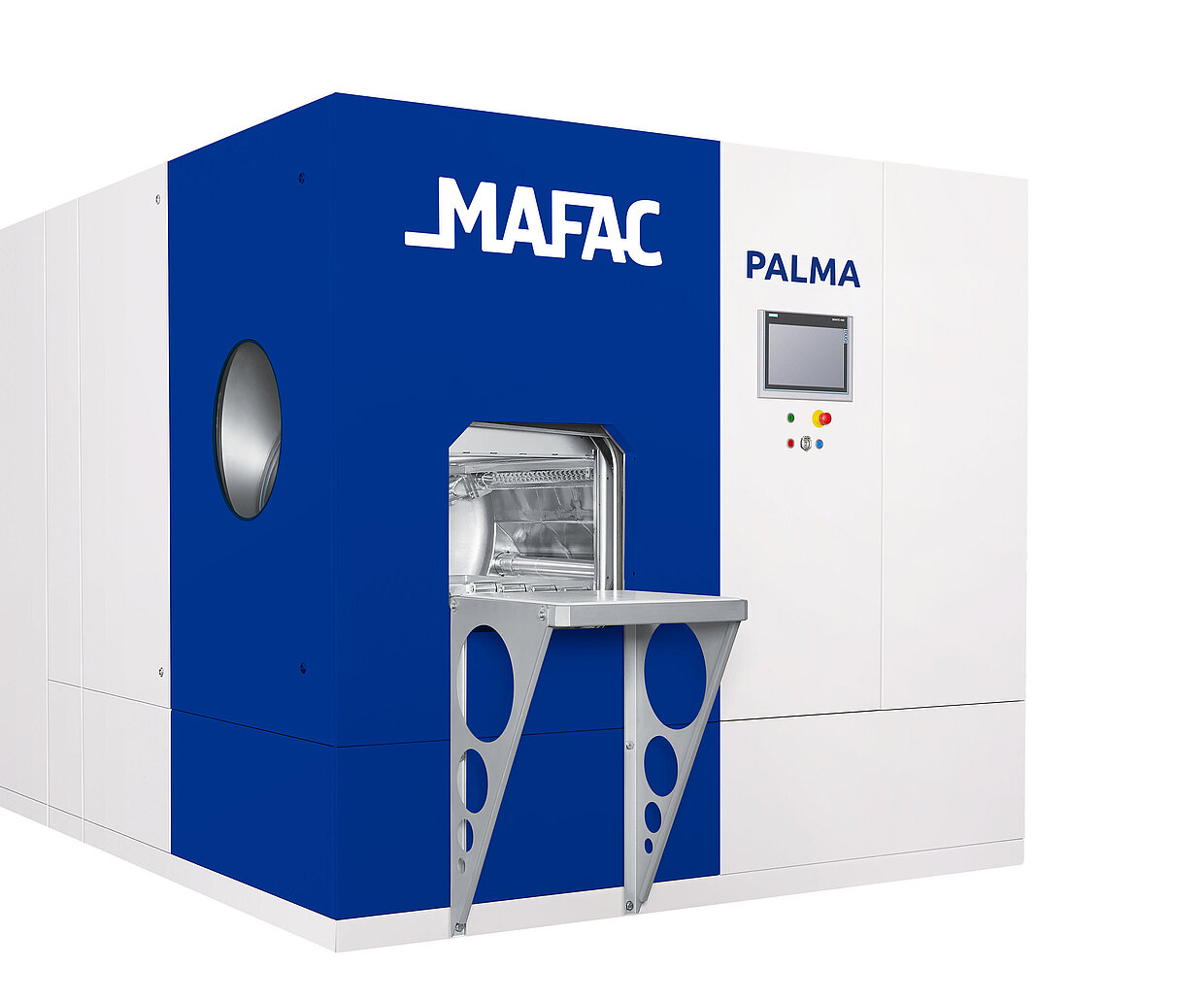
Today, there is a wide range of biodegradable cleaning agents available that provide flexibility in the use of water-based systems – always focused on the high demands of TEM deburring. Cleaning is thorough and gentle, and the use of additives can be reduced to a user-friendly level thanks to the patented MAFAC technologies.
If the parts are then precisely dried – for example with vacuum drying or rotating hot air blowing – they are optimally prepared for the next production steps. And the removal of stubborn residues from thermal deburring is transformed from a challenging task into a reliable, economical process with reproducible results.
Autor: Dipl.-Ing. Tobias Lutz, Application Technician at MAFAC