Vektorkinematics: A new Dimension of cleaning in Motion
Rethinking Cleaning - How Vector Kinematics increases Efficiency and Precision
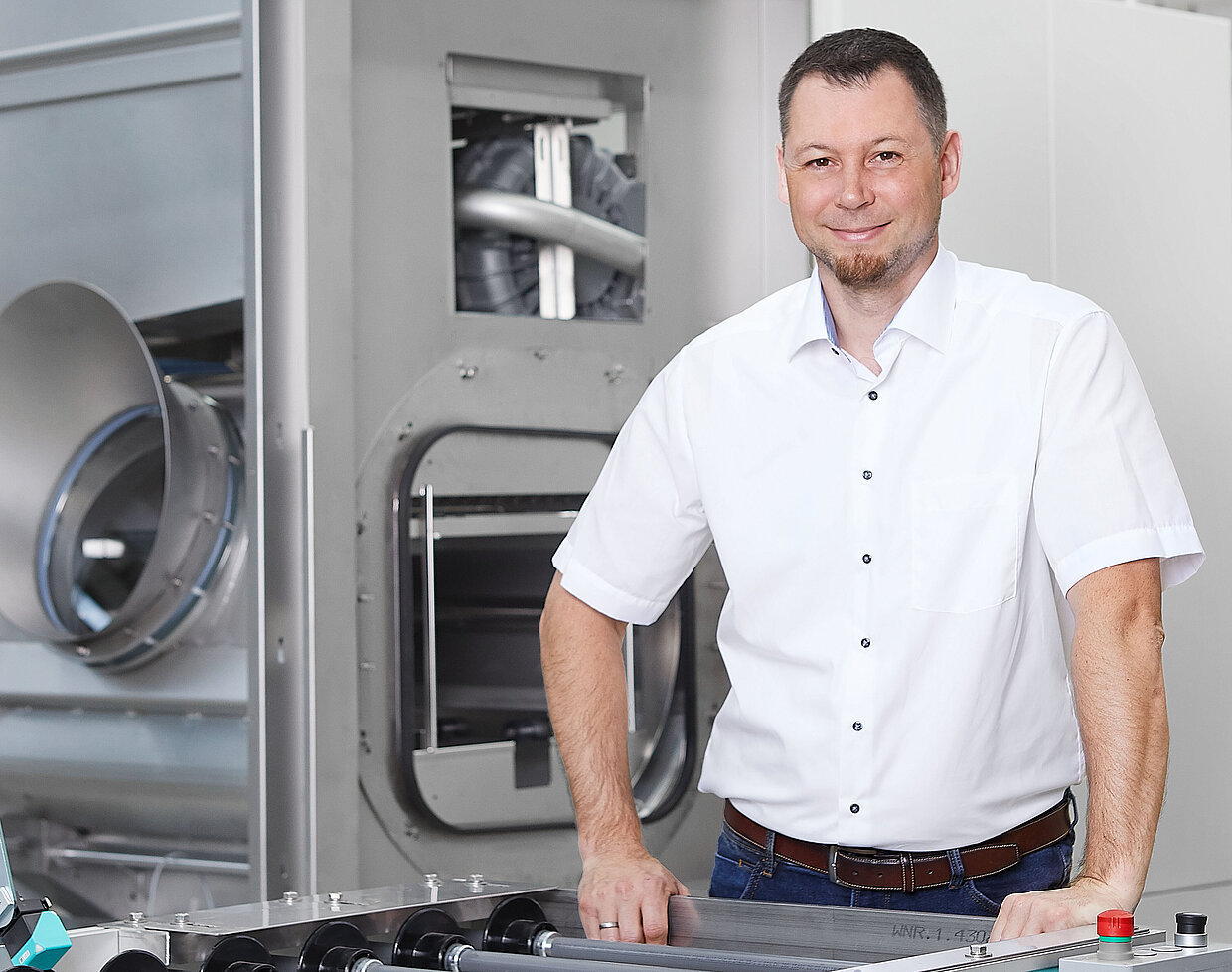
Interview: Dipl.-Ing. Stefan Schaal
Mr. Schaal, what is behind MAFAC Vektorkinematics?
» This is an innovative process for cleaning and drying that provides even more motion during cleaning. It is based on the patented MAFAC technology with counter- or co-rotation of the basket and spray system, and takes the underlying kinematic principle of cleaning in motion many steps further. In other words, we have developed and enhanced the benefits by using targeted turbulence. As a result, workpieces are sprayed more evenly and hard-to-reach areas such as blind holes or undercuts are reached even better.«
Why the term “Vektorkinematics”, it sounds a lot like physics?
» That's exactly what it is, physics. “Vektorkinematics” refers to the directional movements performed by the technology. The term is derived from “vector”, the description of a directional displacement in space. And from “kinematics”, the technical term for movement in mechanics. With MAFAC Vektorkinematics, the motion sequences are interdependent and follow a specific pattern within vector fields. As a result, the flows or turbulences created also follow a pattern of motion. «
How exactly does MAFAC Vektorkinematics work and what is the key difference to kinematic cleaning and drying?
» Here, too, we follow the principle of simultaneous or counter rotation of the nozzle carrier and the basket holder. The key innovation is the additional rocking of the nozzle tube around its own axis by 35° to each side. The rotary movement of the nozzle arm is coupled to this via a cam disk. This creates a swivel movement of the nozzles while the basket pick-up system rotates synchronously. The rotation is independent of each other, creating interesting motion sequences. Another new feature is that the basket and nozzle carrier rotate at an adapted speed. Adapted means that the speed of both rotations is calculated in advance by the software using vector fields. In doing so, the program simulates a motion pattern and derives motion sequences. The result is an optimally coordinated interplay of nozzle tube and basket movement. «
Where does the technology rank compared to other processes for aqueous parts cleaning?
» In brief: We achieve a much higher impact. Until now, most aqueous cleaning processes have used rigid nozzle systems. The nozzle arm is fixed in the cleaning chamber and only sprays at a certain angle into the center of the workpiece carrier. This motion sequence cannot avoid shadow zones, and some areas are insufficiently reached by the spray jet.
Depending on the geometry, the impact on the component surface can vary greatly between the primary and secondary surfaces. MAFAC Vektorkinematics reduces this discrepancy. The nozzles also swivel out to reach further areas from different angles – more precisely, with the previously calculated optimum angle variance. «
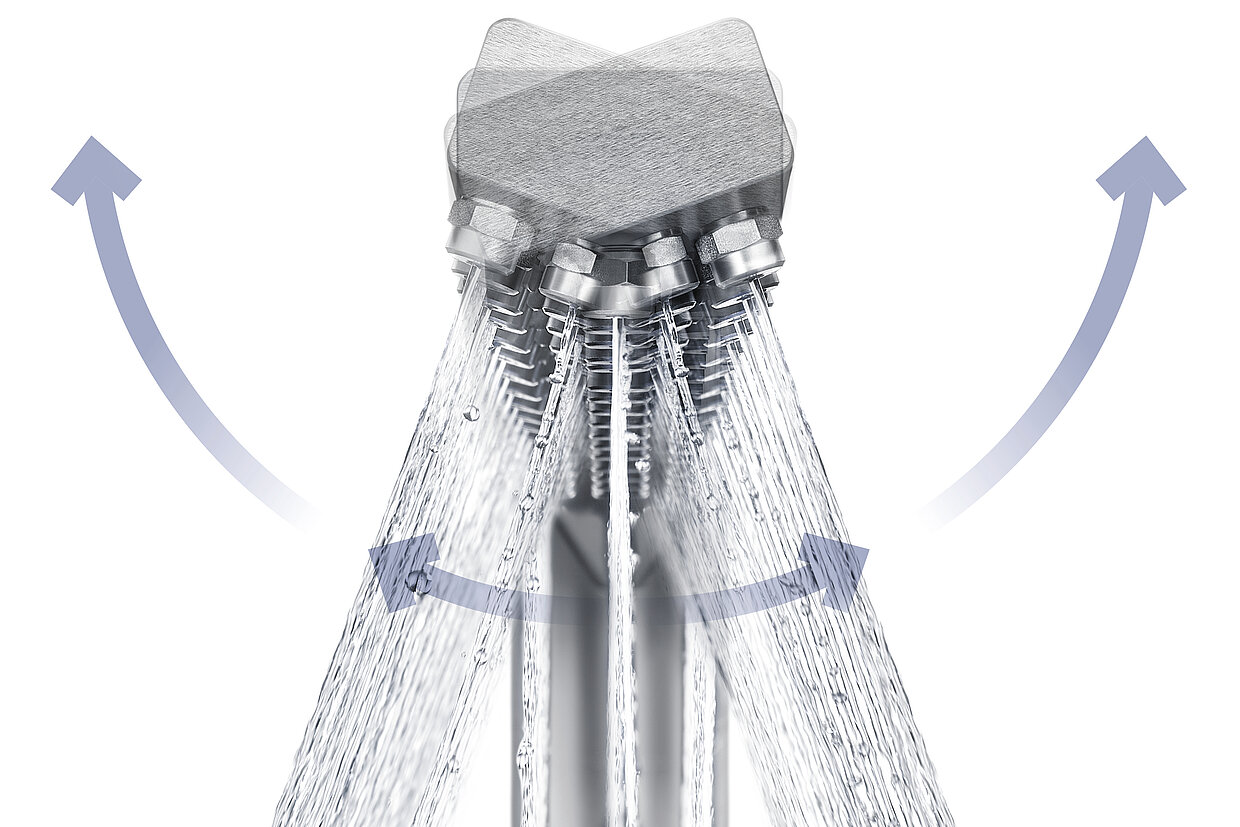
How does the technology work, what are the advantages and benefits for the users?
» Thanks to the improved mechanics and the interaction of the basket and nozzle movement, which is individually and optimally adapted to the components, impact is more targeted and uniform. The speed is automatically calculated by the software according to the time required for the process. The entire process is optimized in terms of time and resources; critical zones are reached not only during flood cleaning, but already during spray cleaning. «
» The effect is up to 60 percent higher for set parts and significantly better for bulk parts. In addition, flood cleaning is more intensive due to greater turbulence in the flow. We also achieve a stronger flow effect during drying thanks to the moving nozzles. There is a greater exchange of heat and material, users clean more efficiently. This is an advantage in the face of increasing cleanliness requirements and tighter budgets. In addition, users can respond much more flexibly to a wide range of parts or to changes in the parts program: Thanks to the high angle variance, very different workpiece batches can be processed. «
What are the main applications for MAFAC Vektorkinematics?
» In addition to the mentioned workpiece batches, the process is recommended for complex components with geometries that are more or less easy to reach, as well as castings with very deep bores and undercuts, either as set parts or as bulk goods. «
Why are you talking about nothing less than a new dimension for cleaning in motion?
» Simply because we have achieved very high optimization values. In my opinion, we are setting a new benchmark in terms of effectiveness compared to the 10 to 15 percent improvements that are customary in this sector. With the individual, software-controlled adaptation options to the component geometry, solutions for previously unprocessed issues can be tackled. This takes parts cleaning as a whole a big step further and opens up many new applications. «
An Interview with: Dipl.-Ing. Stefan Schaal
Managing Partner at MAFAC