Drying as an economic Factor
Efficiency That Pays Off – The Role of Drying in Industrial Parts Cleaning
Drying is an important part of the cleaning process in order to prepare the parts for subsequent production steps or shipping. Only optimally dried parts can be further processed, assembled, packaged, transported or stored without any problems. However, in order to adequately meet the relevant specifications, drying requires time, during which energy is used for heat. This can take up more than 30 percent of the cleaning time - drying often becomes a critical economic factor.
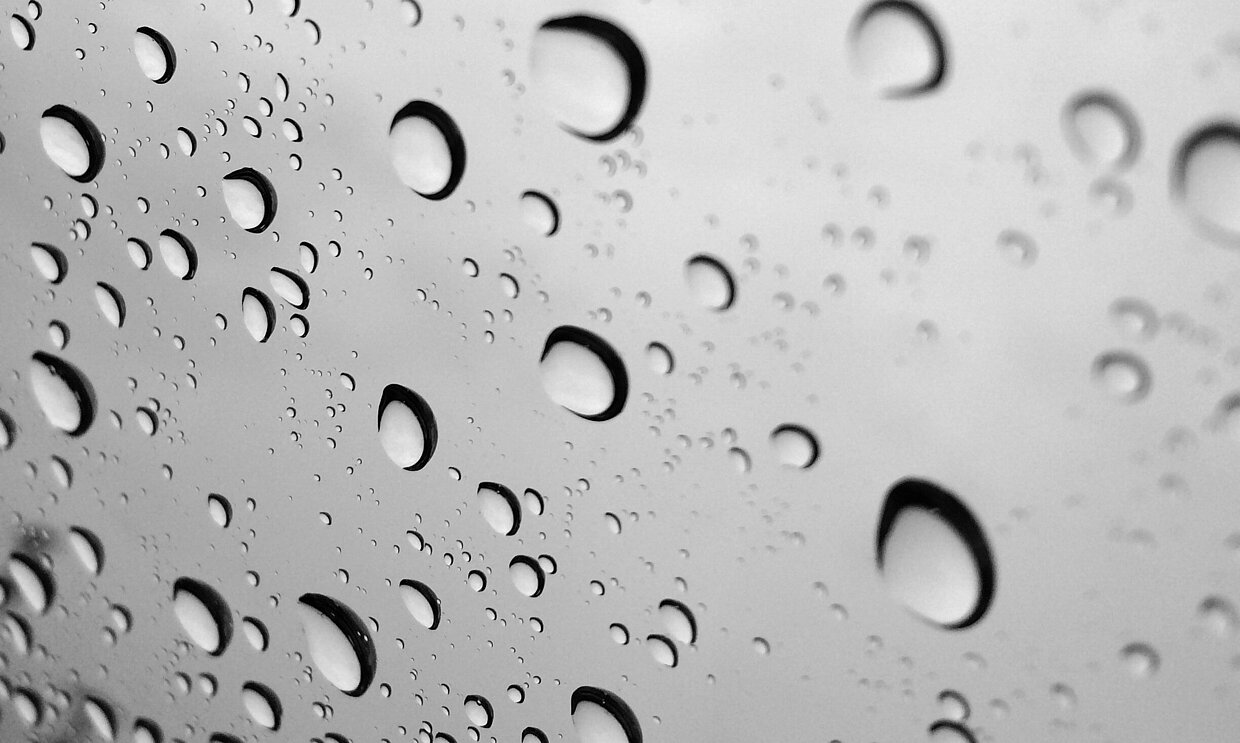

Requirements for drying
In principle, drying is subject to the cleanliness requirements of the respective cleaning task. In the case of aqueous parts cleaning, it is also determined by the relatively high surface tension of the water medium and the geometry and material properties of the components. Large workpieces with a less complex geometry are generally easier to dry than components with scooping topologies such as narrow gaps, deep holes, undercuts or delicate, thin-walled structures.
Batches with bulk material are also challenging for the drying process, as there are many zones that are difficult to reach. The material and its thermal conductivity also determine the drying of the components: Temperature-insensitive, solid metal parts can be dried more quickly than components made of plastic or thin-walled light metals. Furthermore, the higher the surface quality requirements, the longer drying generally takes.
Movement brings efficiency
With increasing cost pressure in the manufacturing industry, effective and economical drying is becoming ever more important. In order to shorten drying times, MAFAC offers the process of rotating flow drying with hot air. This process uses the principle of relative movement and makes the drying process faster and more effective at the same time by means of highly turbulent flow pulses, heat and movement.
To make this possible, the system works with two rotating pipes arranged next to each other: The pulse blow pipe supplies the cleaning chamber with compressed air pulses of up to 6 bar, which act on the components in a specific ratio of pulse and pause. During the drying phase, hot air at a pressure of approx. 250 mbar flows through the nozzle pipe. During drying, both tubes rotate around the workpieces, which rotate in opposite directions in the basket and are directly exposed to pulsating hot air. This combination of impulse blowing, flow drying with hot air and movement creates a highly dynamic interaction and significantly increases the drying performance.
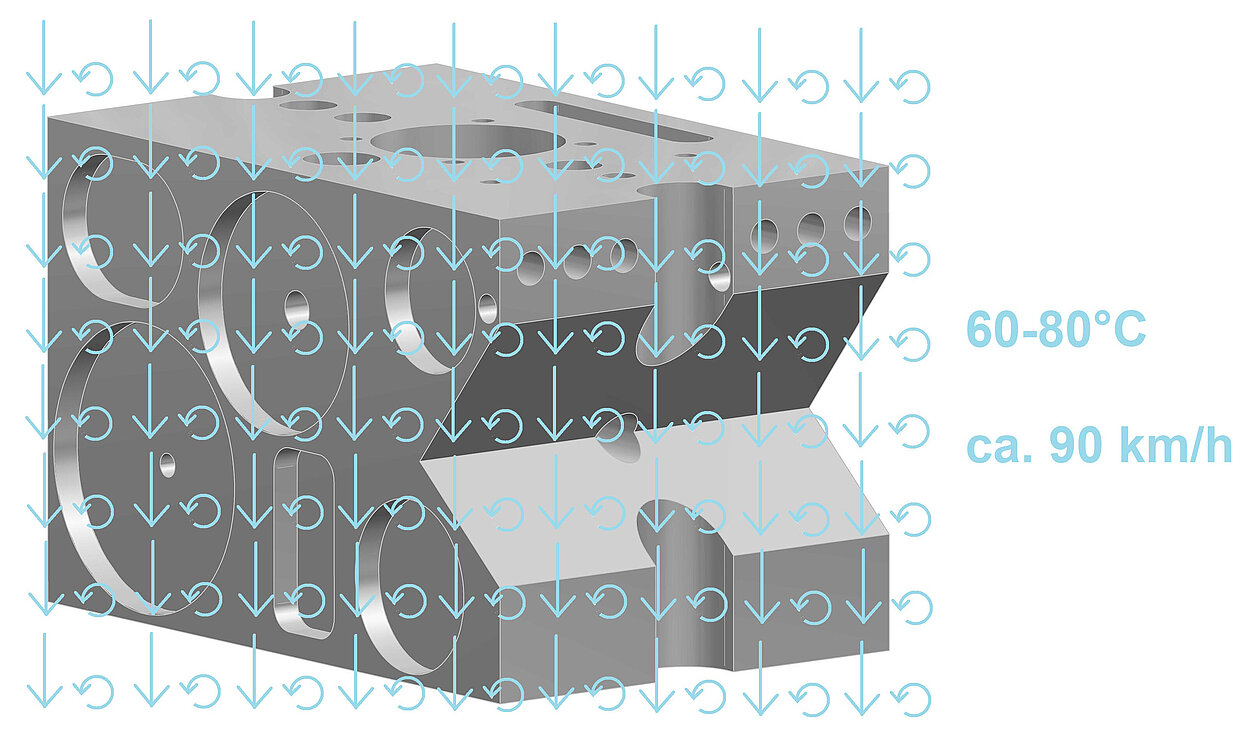
In detail, it works like this: the short bursts of compressed air from the impulse blowing break up any remaining water droplets into many smaller units. This increases the surface area and the water can dry faster. These compressed air pulses are constantly alternating with the hot air flow that passes through the impulse blow pipe during the pauses between pulses. This creates a strong volume flow, the process air reaches the surfaces of the components in a targeted manner and at a constantly high pressure. This interaction results in a high and efficient heat and mass transfer. The turbulent flow leads to a homogeneous temperature distribution in the cleaning chamber.
And, in combination with the impulse force, up to 45 percent better drying performance compared to stationary processes. In addition, the drying time is also reduced by up to 45 percent, depending on the component geometry.
Economical and resource-saving
In addition to the more efficient drying performance, the rotating flow drying system also contributes to reduced energy consumption and thus to an improved CO2 balance. The rotation of the nozzle system and the introduction of hot air exploit synergies from mechanical and thermal flow effects - the combination of high volume flows with fast flow speeds leads to a high evaporation rate. While only around half of the heat reaches the workpiece in stationary processes, the rotating drying system delivers two thirds. At a temperature of 90 degrees, the drying air on the workpiece is eight degrees warmer, which accelerates the entire drying process. The more targeted use of flow pressure, temperature and movement shortens the cycle time of the drying phase and thus the entire cleaning process.
Autor:
Dipl.-Ing. Stefan Schaal
Managing Director MAFAC