MAFAC Cleaning Technologies: Physics over Solvents!
MAFAC is cleaning with motion, using physics instead of chemistry: The basket with the parts rotates and the spray system rotates simultaneously. The cleaning medium – water and additive – impinges dynamically on the products from different directions and can act uniformly everywhere. Cleaning is product sensitive and highly efficient, both on surfaces and in areas difficult to reach.
Cleaning is done product sensitive and highly efficient, both on surfaces and in areas difficult to reach. The water clear advantages for you: faster cleaning with reproducible best results, targeted drying, high process reliability and sustainability.
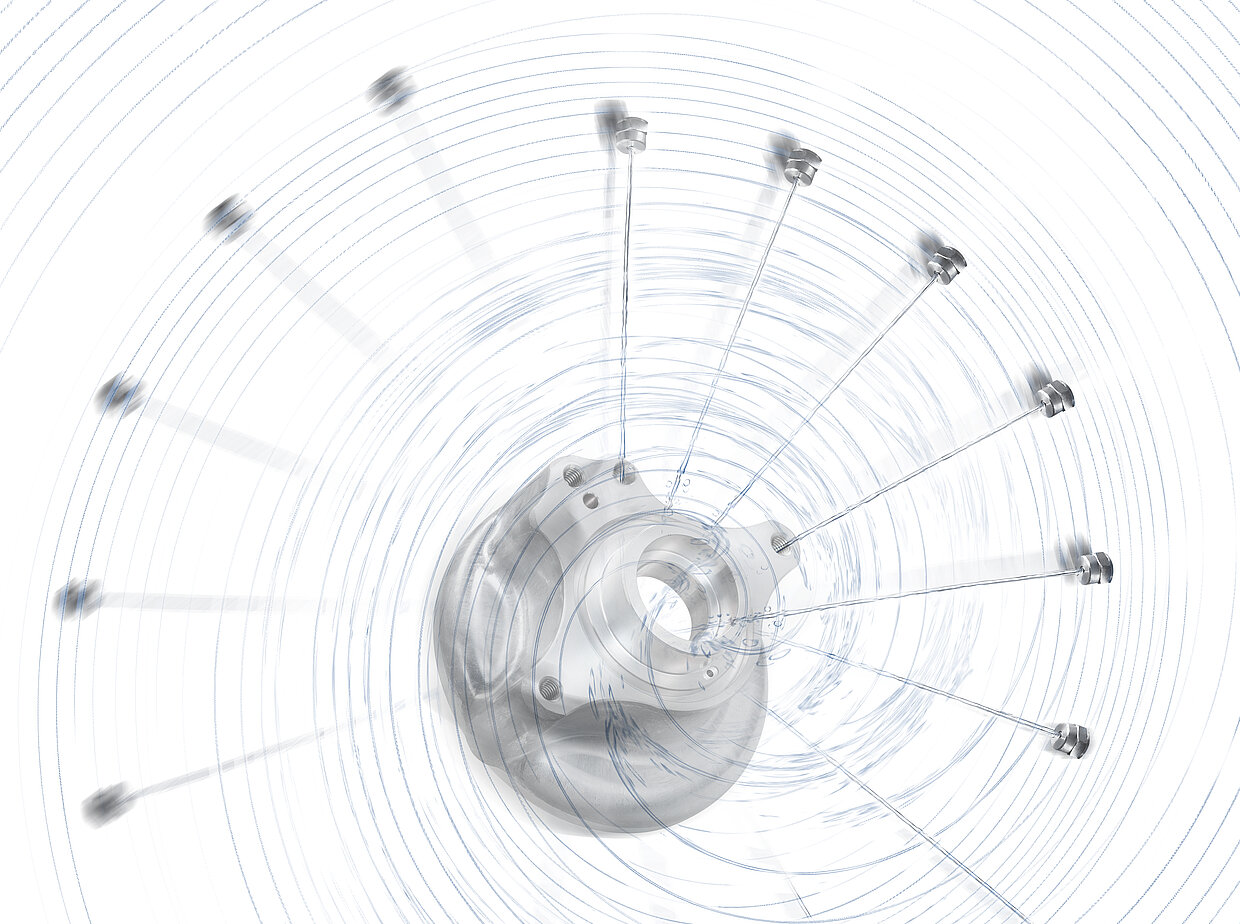
Technologies with water-clear Benefits:
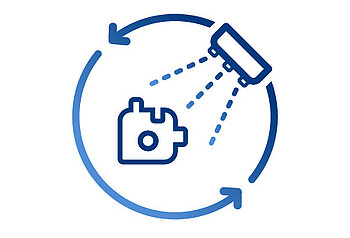
Patented basic technology for cleaning and drying of uncomplicated workpieces. With simultaneous rotation of spray system and cleaning objects.
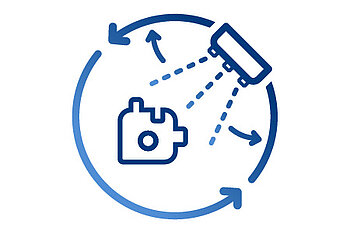
The next dimension for complex geometries: Rotation and swiveling in combination. For increased versatility and improved results already in spray cleaning.
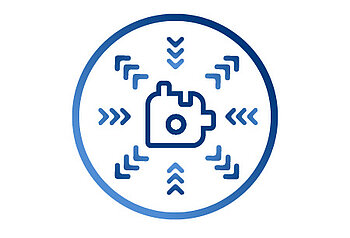
Patented technology with pressure changes for highest demands and industry standards. For optimized cleanliness of hard-to-reach areas and tight structures.
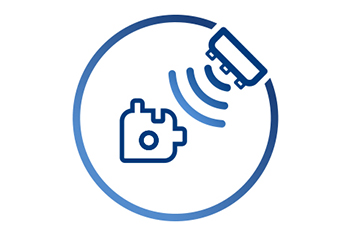
Deep cleaning with rotation of basket, water jet and ultrasonics. For maximum film and particle removal on complex, finely structured components.